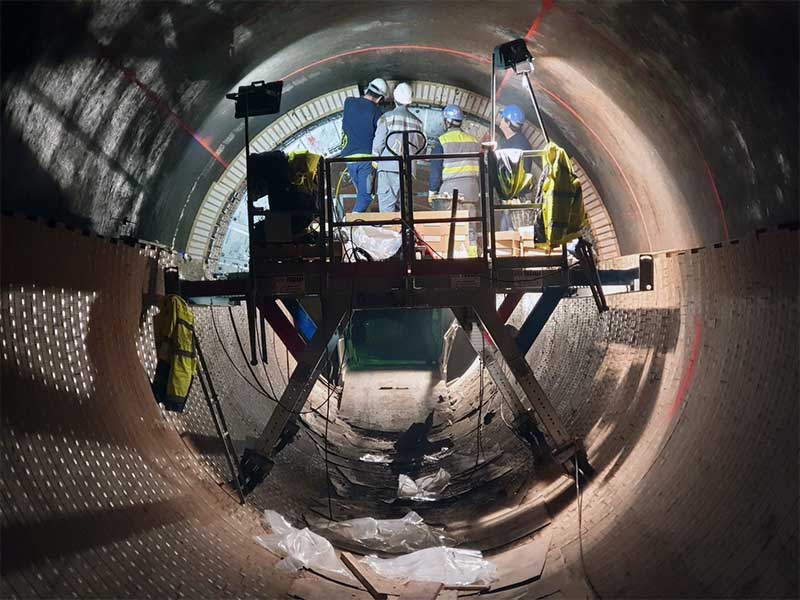
Refractory materials are specifically designed to withstand high temperatures, chemical attacks, and mechanical stresses in industries such as steel, cement, petrochemicals, and more. They provide critical insulation and protection to industrial furnaces, kilns, reactors, and other high-temperature equipment. However, the benefits of refractory materials can only be fully realized if they are installed correctly.
1. Selecting the Right Refractory Materials:
Proper installation begins with choosing the right refractory materials for a specific application. Factors such as operating temperature, type of chemical exposure, abrasion resistance, and thermal conductivity should be considered during material selection. Collaborating with experienced refractory suppliers like Pennekamp Middle East can ensure that you receive expert guidance in selecting the most suitable refractory materials for your needs.
2. Preparation of Installation Surface:
To ensure a solid bond between the refractory lining and the substrate, the installation surface must be thoroughly prepared. This involves cleaning, removing any contaminants, and repairing any damaged areas. The surface should be free from oils, paints, old refractory material, and other substances that may hinder proper adhesion. Proper surface preparation is essential for achieving optimal performance and preventing premature failure.
3. Correct Mixing and Application Techniques:
Refractory materials often come in the form of dry mixes or slurries that need to be mixed with water or other binders before application. Accurate proportioning and thorough mixing of these materials are vital to achieve uniformity and consistency. The mix should be properly tested for the desired viscosity, workability, and flow characteristics. Following the manufacturer’s instructions and using the appropriate application methods, such as spraying, troweling, casting, or gunning, is crucial for achieving the desired density, thickness, and integrity of the refractory lining.
4. Proper Curing and Drying:
After application, refractory linings need adequate time to cure and dry before being subjected to high temperatures. Proper curing ensures the development of desirable physical properties and chemical bonds within the refractory material. Following the manufacturer’s recommended curing time and temperature profiles is essential to achieve the desired strength and minimize the risk of thermal stresses or cracking during subsequent heating cycles.
5. Regular Inspection and Maintenance:
Once the refractory lining is installed, regular inspections and maintenance are crucial for early detection of any issues or signs of deterioration. Thermal cycling, chemical attacks, mechanical stress, and operational wear can all impact the performance of refractory linings over time. Routine inspections and timely repairs or replacements can extend the service life of refractory products, improve process efficiency, and minimize costly downtime.
Proper installation techniques are of paramount importance when it comes to refractory products. From selecting the appropriate materials to meticulous surface preparation, correct mixing and application, and adequate curing and drying, each step contributes to the overall performance and longevity of refractory linings. By partnering with an experienced refractory supplier like Pennekamp Middle East, you can ensure that your installations are carried out with precision and expertise, maximizing the efficiency and durability of your refractory products.
For all your refractory needs, trust Pennekamp Middle East, a leading supplier of high-quality refractory raw materials and finished products. Contact us today to discuss your requirements and benefit from our expertise in