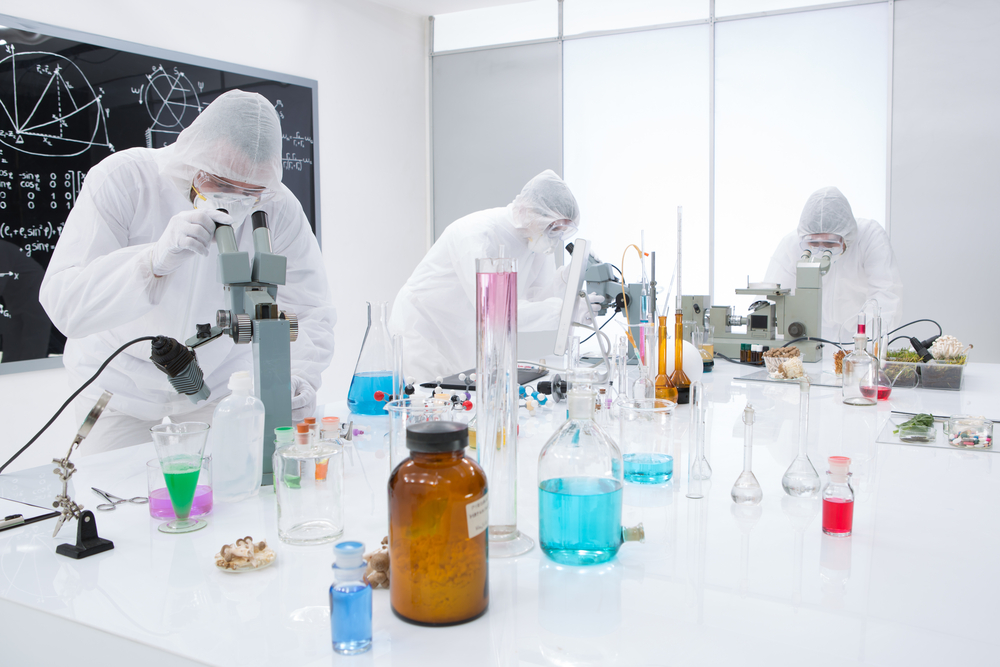
As industries continue to evolve, so do the materials and products that support them. Refractory products are no exception, as manufacturers are constantly seeking new ways to improve their performance, durability, and sustainability. In this blog post, we’ll take a closer look at the emerging trends and innovations in refractory product development, and how they’re shaping the future of the industry.
The Importance of Research and Development
In order to stay ahead of the curve, refractory manufacturers must invest heavily in research and development (R&D). This includes exploring new materials, testing new formulations, and experimenting with different manufacturing processes. R&D allows manufacturers to identify new opportunities and optimize existing products, improving their quality, performance, and cost-effectiveness.
Emerging Trends in Refractory Product Development
One of the biggest trends in refractory product development is the use of advanced materials, such as ceramics and composites. These materials offer greater strength and durability than traditional refractories, making them ideal for high-temperature and high-wear applications. Additionally, advanced materials can be engineered to have specific properties, such as thermal conductivity and chemical resistance, which can be tailored to meet the needs of specific industries and processes.
Another emerging trend is the use of automation and digitalization in refractory manufacturing. By using advanced technologies such as artificial intelligence, machine learning, and robotics, manufacturers can improve their production efficiency, reduce waste, and ensure greater consistency in their products. This can also lead to greater safety in manufacturing processes, as robots can be used to handle hazardous materials and perform dangerous tasks.
Innovations in Refractory Product Design
In addition to advanced materials and automation, manufacturers are also exploring new designs and geometries for refractory products. For example, the use of 3D printing technology allows manufacturers to create complex shapes and structures that were previously impossible with traditional manufacturing techniques. This can lead to improved performance and efficiency in industrial processes, as well as cost savings due to reduced waste and scrap.
Another innovation in refractory product design is the use of coatings and surface treatments. These treatments can improve the properties of existing materials, such as thermal shock resistance, chemical resistance, and erosion resistance. This can extend the life of refractory products and reduce the need for frequent replacements.
The Future of Refractory Product Development
As refractory manufacturers continue to invest in R&D and explore emerging trends and innovations, the future of the industry looks bright. We can expect to see continued improvements in performance, durability, and sustainability, as well as greater customization and flexibility to meet the needs of specific industries and processes.
At Pennekamp Middle East, we are committed to staying at the forefront of refractory product development. With a team of experienced engineers and a state-of-the-art R&D facility, we are constantly exploring new materials, designs, and manufacturing processes to improve our products and meet the evolving needs of our customers. Contact us today to learn more about our cutting-edge refractory solutions.