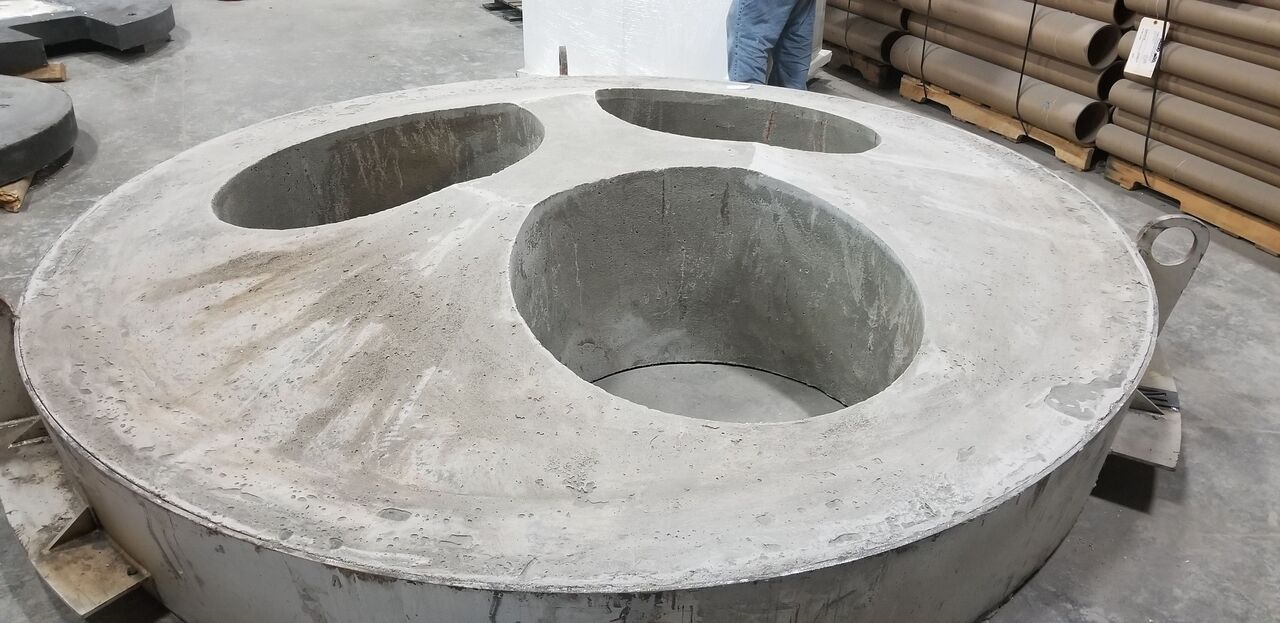
Precast refractory shapes are pre-formed pieces of refractory material that are molded in a factory and then shipped to the installation site. They are designed to fit specific areas of a furnace, kiln, or other high-temperature process equipment, providing a more precise and efficient installation. Precast shapes can be customized to meet specific process requirements, such as increased thermal conductivity, erosion resistance, or thermal shock resistance.
One of the key benefits of using precast refractory shapes is the reduction in installation time and labor costs. Traditional refractory installation involves manually forming and placing bricks, which can be a time-consuming and labor-intensive process. Precast shapes eliminate the need for bricklaying, which can reduce installation time and labor costs by up to 50%.
Precast shapes also offer improved performance compared to traditional brick installations. Since precast shapes are molded in a factory, they are subject to strict quality control measures, resulting in consistent quality and performance. They can be designed to fit tightly together, minimizing gaps and reducing the risk of heat loss and hot spots.
Another cost-effective benefit of precast refractory shapes is their durability and longevity. Precast shapes are often made from high-quality refractory materials that are more resistant to wear, erosion, and thermal shock than traditional bricks. This increased durability can reduce the frequency of repairs and replacements, leading to long-term cost savings.
In addition to their cost-saving benefits, precast refractory shapes also offer environmental benefits. They produce less waste than traditional brick installations since they are custom-made to fit specific areas, reducing the need for cutting and shaping. Precast shapes can also be made from eco-friendly materials, such as recycled refractory materials or sustainable raw materials.
In conclusion, precast refractory shapes offer a cost-effective solution for improving refractory performance and reducing costs in high-temperature industrial processes. They offer improved performance, reduced installation time and labor costs, increased durability and longevity, and environmental benefits. Pennekamp Middle East offers a range of precast refractory shapes and can work with you to customize shapes to meet your specific process requirements. Contact us today to learn more about how precast refractory shapes can benefit your industrial process.
Contact us today to learn more about our precast refractory shapes and how they can benefit your industrial process. Our team of experts can work with you to customize shapes to meet your specific process requirements.