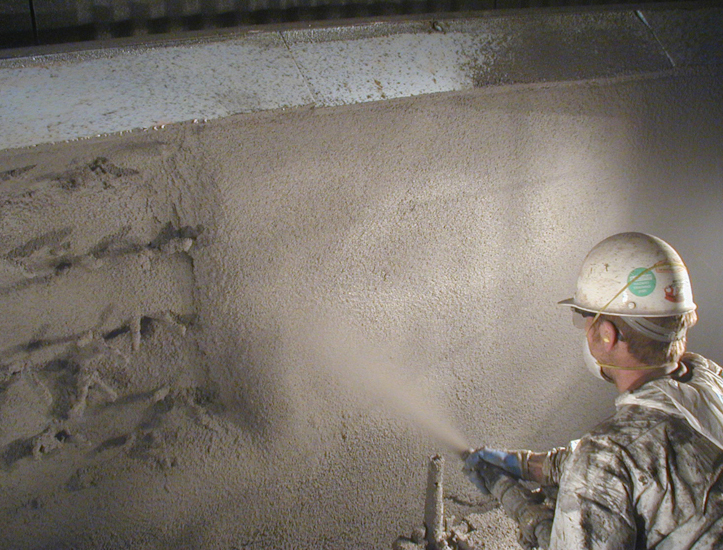
When it comes to boiler applications, the choice of refractory materials can significantly impact overall performance and maintenance costs. Traditional refractory bricks have long been a staple in boiler linings, but in recent years, refractory monolithics have gained prominence due to their numerous advantages. In this blog post, we will delve into the world of refractory monolithics, exploring how they are revolutionizing boiler applications.
What Are Refractory Monolithics?
Refractory monolithics, also known as monolithic refractories, are unshaped refractory materials. Unlike traditional bricks or shaped refractories, monolithics are applied in a plastic, wet, or dry form and then cured in place. These materials consist of aggregates, binders, and additives that, when mixed and properly installed, create a seamless, uniform lining within the boiler.
Now, let’s explore the advantages of using refractory monolithics in boiler applications:
One of the primary advantages of refractory monolithics is their ability to provide superior thermal insulation. Monolithic materials can be tailored to specific boiler designs, ensuring a tight and consistent fit. This tight fit minimizes heat loss, resulting in enhanced thermal efficiency. Improved insulation means that boilers require less fuel to maintain the desired temperature, ultimately reducing energy consumption and operating costs.
Compared to traditional refractory bricks, which require meticulous placement and skilled labor, monolithic refractories offer a quicker installation process. The wet or plastic forms can be easily applied, tamped, or gunned into place, significantly reducing downtime during boiler maintenance or repairs. This time-saving aspect translates to cost savings, as shorter installation times mean less disruption to production schedules.
Boilers often undergo rapid temperature changes during their operational cycles. Refractory monolithics are renowned for their exceptional thermal shock resistance, as they can withstand sudden temperature fluctuations without cracking or spalling. This durability ensures a longer lifespan for the refractory lining, reducing the need for frequent repairs or replacements.
Many boiler applications involve exposure to corrosive environments due to the nature of the materials processed or the combustion byproducts. Refractory monolithics can be engineered to resist corrosion effectively. The addition of specialized additives can create a protective barrier, reducing the risk of material degradation and extending the lifespan of the boiler lining.
Refractory monolithics offer a high degree of customization. Manufacturers can tailor the composition of monolithic materials to suit specific boiler requirements, including temperature ranges, chemical resistance, and mechanical strength. This flexibility ensures that the refractory lining is precisely optimized for the intended application, enhancing overall performance.
The durability and longevity of refractory monolithics contribute to a significant reduction in maintenance costs over time. With fewer repairs and replacements required, boiler operators can allocate resources more efficiently, focusing on optimizing production processes rather than addressing refractory issues.
Safety is a paramount concern in industrial settings, and refractory monolithics play a crucial role in enhancing boiler safety. Their ability to withstand extreme temperatures and thermal shock minimizes the risk of unexpected failures that could lead to accidents, downtime, or environmental hazards.
As industries increasingly prioritize sustainability, refractory monolithics offer eco-friendly advantages. Their energy-efficient properties reduce fuel consumption, contributing to lower carbon emissions. Additionally, the longer service life and reduced need for replacements result in less waste and a smaller environmental footprint.
Incorporating refractory monolithics into boiler applications is a strategic choice that can revolutionize your industrial processes. To experience firsthand the advantages of these innovative materials, partner with Pennekamp Middle East, your trusted source for high-quality refractory solutions. Contact us today to explore customized refractory monolithic options tailored to your specific boiler needs and start reaping the benefits of enhanced efficiency, reduced maintenance costs, and improved sustainability. Elevate your boiler performance with Pennekamp Middle East – your partner in refractory excellence.