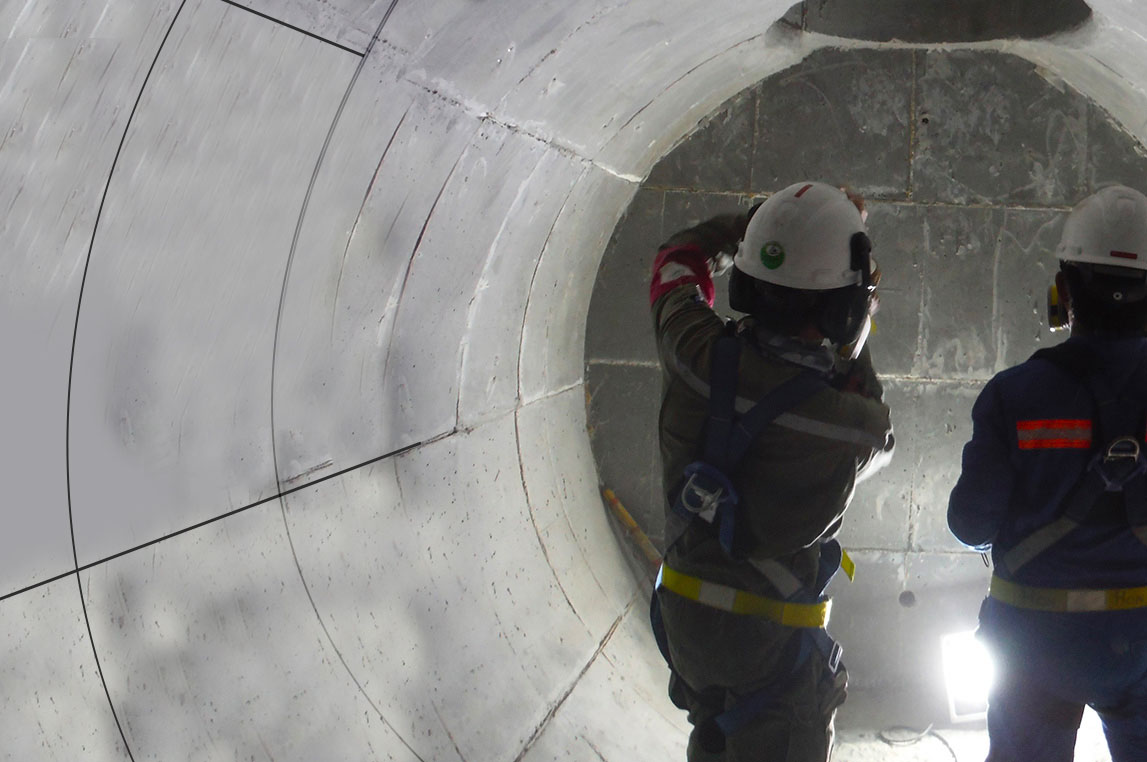
Refractory products play a crucial role in industries such as steel manufacturing, petrochemicals, and aerospace. They are the unsung heroes that withstand extreme temperatures, chemical reactions, and mechanical stress to ensure the smooth operation of various industrial processes. But have you ever wondered what goes into the design of these remarkable materials? Join us as we delve into the fascinating science behind refractory product design.
Understanding the Science of Refractory Materials
Refractory materials are engineered to withstand high temperatures and harsh environments, making them indispensable in industries that rely on extreme heat and chemical resistance. The science behind these materials involves a careful selection of raw materials and a deep understanding of the physical and chemical properties that allow them to perform under duress.
– Refractory raw materials are chosen based on their ability to withstand specific operating conditions. Common raw materials include alumina, magnesia, silica, and zirconia, each offering unique properties.
– Alumina, for instance, is known for its high-temperature resistance and exceptional mechanical strength, making it ideal for applications such as furnace linings and crucibles.
– Magnesia, on the other hand, excels in environments with high basicity due to its excellent resistance to alkaline compounds.
– Once the raw materials are selected, they are precisely mixed in specific proportions to achieve the desired refractory properties.
– The mixture is then carefully bonded using various techniques, including additives, binders, and water to create a workable refractory product.
– The refractory mixture is shaped into various forms such as bricks, castables, or fibers, depending on the intended application.
– Curing involves controlled drying and heating processes to strengthen the refractory structure and remove any remaining moisture.
– The final step is firing the shaped refractory product in kilns at high temperatures to enhance its structural integrity.
– Quality control measures are implemented to ensure that the finished product meets the required standards for thermal conductivity, density, and chemical resistance.
The science behind refractory product design is a complex and meticulous process that combines material science, engineering expertise, and a deep understanding of industrial needs. It is through this scientific approach that Pennekamp Middle East delivers high-quality refractory raw materials and finished products to meet the demands of various industries.
Are you looking for reliable refractory solutions tailored to your industry’s needs? Contact Pennekamp Middle East today to explore our range of refractory materials and products designed to withstand the harshest industrial conditions. Our team of experts is ready to assist you in finding the perfect refractory solution for your specific requirements. Don’t compromise on quality – partner with Pennekamp Middle East for superior refractory products.