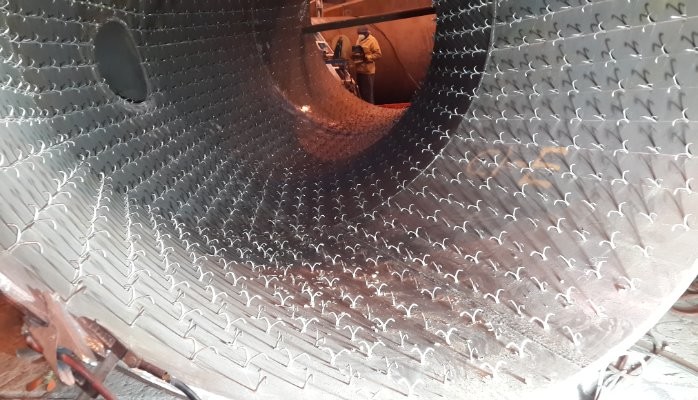
Introduction
In high-stress industrial environments, where temperatures soar and materials face extreme conditions, the choice of refractory materials is critical. Refractory plastics, also known as refractory castables or refractory mortars, are engineered to address these challenges with remarkable performance. This blog delves into the properties and advantages of refractory plastics, their applications in high-stress scenarios, and how they contribute to improved efficiency and durability in demanding industrial settings.
What Are Refractory Plastics?
Refractory plastics are advanced refractory materials that can be shaped and applied like a plastic material before curing. They are composed of a blend of high-temperature resistant aggregates, binders, and additives, designed to withstand severe conditions. Unlike traditional refractory bricks, refractory plastics are applied in a liquid or paste form, allowing for versatile use in complex geometries and high-stress areas.
Properties of Refractory Plastics
Benefits of Using Refractory Plastics
Applications in High-Stress Environments
Conclusion
Refractory plastics offer a versatile and high-performance solution for high-stress industrial applications. Their exceptional temperature resistance, thermal shock resistance, mechanical strength, and chemical resistance make them ideal for demanding environments. By enhancing durability, improving efficiency, and reducing downtime, refractory plastics contribute to the optimal performance and longevity of industrial equipment. At Pennekamp Middle East, we are dedicated to providing advanced refractory plastics tailored to meet the specific needs of your high-stress applications, ensuring superior performance and reliability in every operation.