Porosity refers to the presence of tiny voids or pores within a material, and it is a fundamental characteristic of all refractory materials. These pores can be open or closed, and their size, distribution, and connectivity significantly influence the properties and performance of the refractory product. In the context of refractories, porosity is a key factor in determining how the material behaves in high-temperature environments, such as furnaces, kilns, and reactors.
How Porosity Affects Refractory Performance
- Thermal Conductivity and Insulation: One of the primary roles of refractories is to provide thermal insulation, protecting both the equipment and surrounding environment from extreme temperatures. Porosity influences how well a refractory material insulates against heat. High porosity typically leads to lower thermal conductivity, making the material an effective insulator. However, excessively high porosity can compromise the material’s strength and durability, leading to premature failure. The right balance of porosity is necessary for optimal thermal performance.
- Resistance to Thermal Shock: Thermal shock occurs when a material experiences rapid temperature changes, causing it to expand or contract unevenly. Porosity plays a significant role in a refractory’s ability to withstand thermal shock. Materials with low porosity are less likely to crack or deform when exposed to sudden temperature shifts, while highly porous materials may be more vulnerable to thermal stress. Managing porosity is key to ensuring that refractories remain durable under challenging operating conditions.
- Slag and Chemical Corrosion Resistance: In industrial applications, refractories are often exposed to aggressive molten metals, slags, and gases that can cause erosion and chemical wear. Porosity affects the material’s resistance to chemical attack. While some porosity is necessary for improving resistance to slag penetration, excessive porosity can increase the surface area that comes into contact with corrosive substances, accelerating the material’s degradation. A controlled, optimized level of porosity ensures that refractories maintain their integrity while resisting corrosion.
- Mechanical Strength: The mechanical strength of refractory materials is influenced by their porosity. High porosity generally weakens the material’s mechanical properties, making it more susceptible to wear and mechanical failure. On the other hand, a well-balanced level of porosity allows for flexibility and strength, ensuring that the refractory material can endure physical stresses without compromising its integrity.
- Heat Storage and Energy Efficiency: In certain applications, the ability of a refractory material to store and release heat efficiently is crucial for energy conservation. Porosity affects this heat storage capability. A material with an optimized pore structure can absorb and retain heat effectively, releasing it gradually, which is beneficial for processes that require sustained heat over long periods. This contributes to energy efficiency and reduces the need for constant heating, helping industrial operations save energy and reduce costs.
How Pennekamp Middle East Manages Porosity in Refractory Materials
At Pennekamp Middle East, we understand that the right balance of porosity is essential for maximizing the performance and lifespan of refractory materials. Our advanced manufacturing processes ensure that our products have the ideal porosity characteristics for each application. Whether it’s for steel production, cement manufacturing, or non-ferrous metals processing, we tailor the porosity of our refractories to meet the specific requirements of each industry.
We use cutting-edge techniques to control the pore size, distribution, and connectivity of our refractories. By doing so, we ensure that our materials deliver:
- Optimal thermal insulation to maintain temperature control and reduce energy consumption.
- Superior resistance to thermal shock to extend the lifespan of your equipment and reduce downtime.
- Excellent slag and chemical corrosion resistance to protect against wear and tear in aggressive environments.
- Strong mechanical strength to withstand the physical stresses encountered during industrial operations.
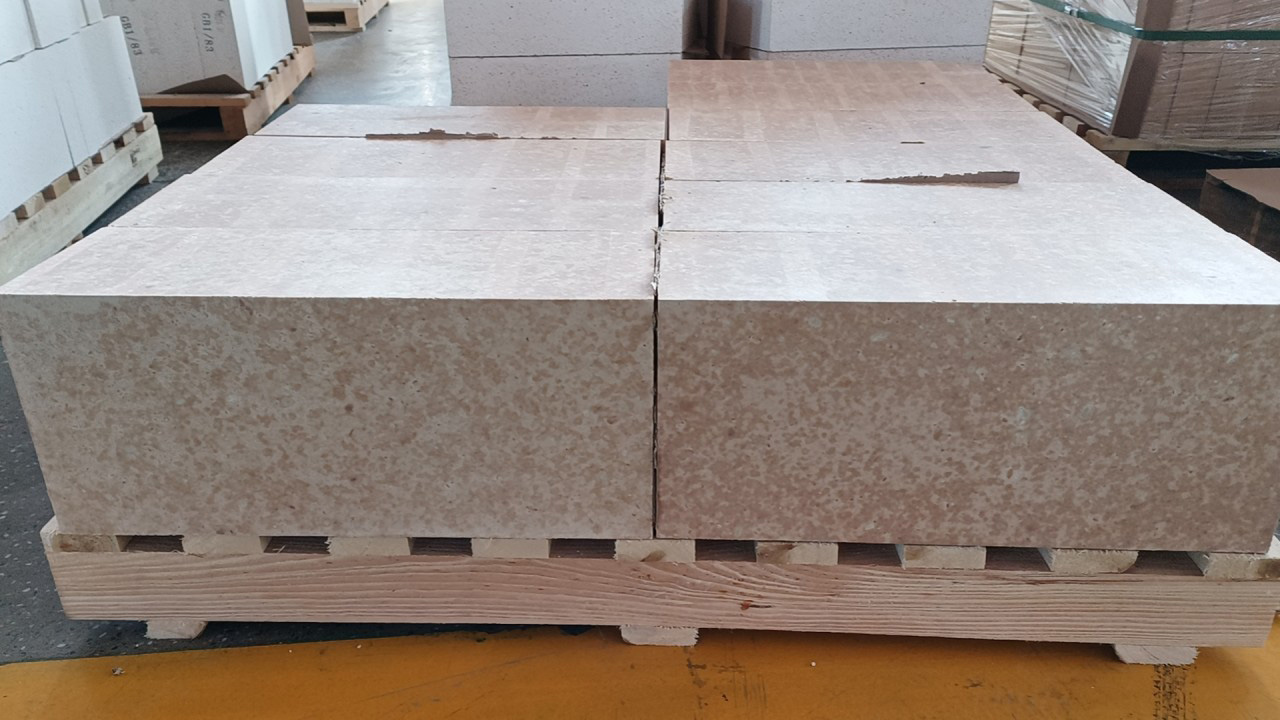
Conclusion: The Critical Role of Porosity in Refractory Materials
Porosity is a key determinant of the performance and durability of refractory materials. It influences various critical properties, including thermal conductivity, resistance to thermal shock, slag corrosion, mechanical strength, and energy efficiency. By understanding and optimizing porosity, we can create refractories that not only meet but exceed industry demands, ensuring long-lasting performance in high-temperature environments.
At Pennekamp Middle East, we specialize in delivering high-quality, tailored refractory solutions that offer the perfect balance of porosity for your specific needs. Whether you’re looking to improve efficiency, reduce operational costs, or enhance equipment longevity, our refractories are engineered to help you achieve your goals.
Contact Pennekamp Middle East today to learn more about how our refractory solutions can improve your operations and contribute to your business’s success.