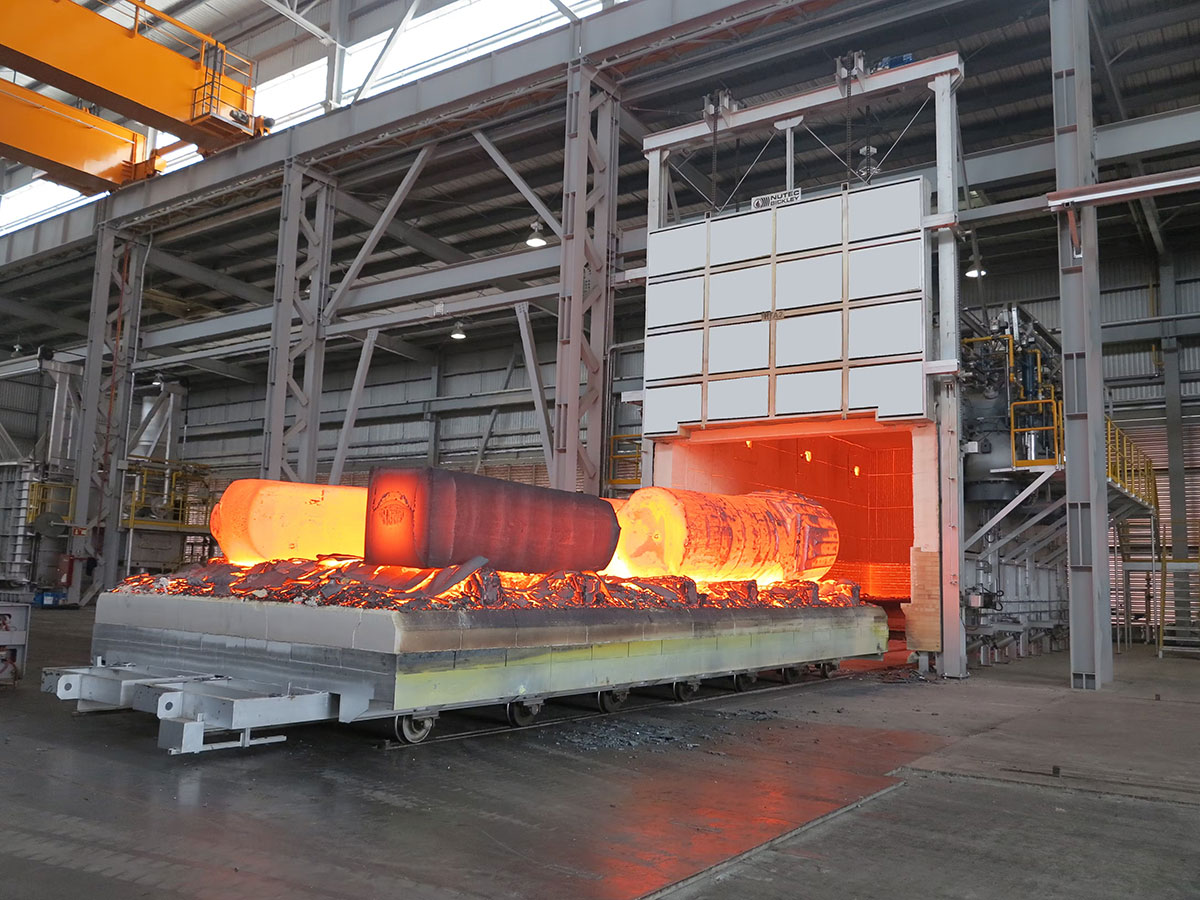
Why Refractory Linings Matter
Industrial furnaces operate under some of the most demanding conditions — intense temperatures, corrosive slags, and constant thermal cycling. Without proper protection, the furnace shell would deteriorate rapidly, leading to costly shutdowns and frequent repairs.
Refractory linings serve as a barrier between the furnace’s internal processes and its outer steel shell. They not only provide thermal insulation but also ensure the structure withstands physical and chemical stresses over time.
Key Benefits of Refractory Linings
Types of Refractory Linings
Design and Installation: The Foundation of Durability
Choosing the right refractory material is just the beginning. Design, thickness, layering, expansion joints, and anchoring systems all play a role in how well a lining performs. Poor installation can shorten the service life significantly, while precision installation can extend it.
At Pennekamp Middle East, we provide technical support to ensure proper selection, lining design, and installation guidance — all essential steps to help our clients get the most out of their furnaces.
Monitoring, Maintenance, and Repair
Refractory linings need regular inspection. Cracks, hotspots, or erosion should be addressed before they escalate into bigger problems. Pennekamp also offers hot-repair mixes and quick-setting materials that allow for on-site maintenance with minimal downtime.
Supporting Efficiency and Sustainability
In today’s industries, energy efficiency and reduced emissions are vital. Refractory linings help by maintaining thermal efficiency and minimizing fuel consumption. Durable linings also reduce waste and material usage over time, supporting more sustainable operations.
Partner with Pennekamp Middle East
At Pennekamp Middle East, we supply a full range of refractory products — from high-grade bricks and castables to mortars and insulating solutions — tailored for applications in BOF, EAF, ladle furnaces, charge ladles, and tundish systems. Our materials are selected for quality, longevity, and performance in high-temperature environments.
Let us help you extend the life of your industrial furnaces and enhance your plant’s performance with trusted refractory solutions. Reach out to our team to learn more or to request a custom product recommendation.