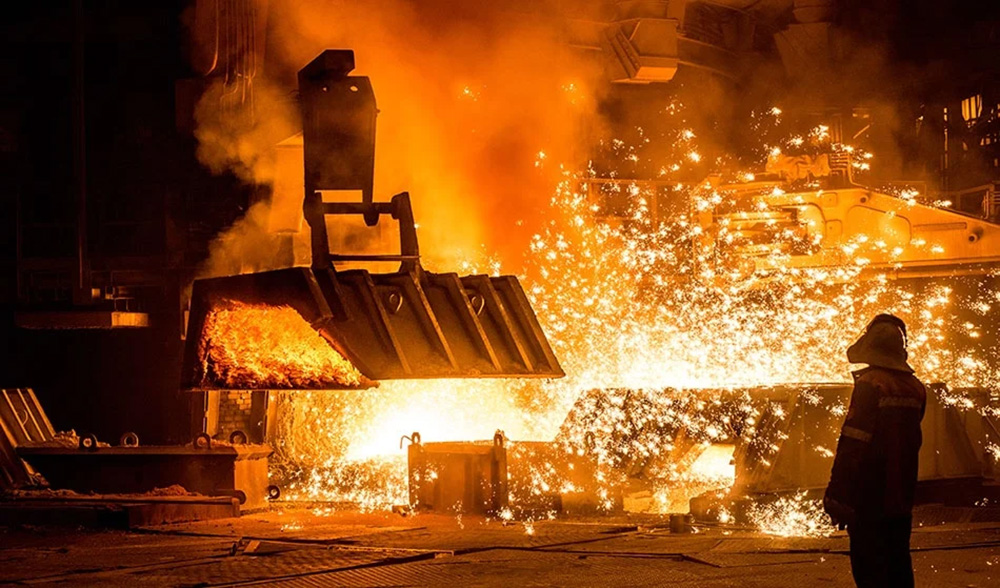
The industrial landscape thrives on pushing boundaries. From forging metals at immense pressures to refining chemicals under extreme conditions, various processes rely on specialized materials to withstand these harsh environments. Refractory materials play a vital role in these high-pressure applications, acting as the silent guardians that ensure operational efficiency and safety.
Understanding Refractory Materials:
Refractory materials are a unique class of materials specifically designed to withstand exceptionally high temperatures – typically exceeding 1000°C. However, their value extends beyond just thermal resistance. In high-pressure applications, refractories offer a crucial combination of properties:
Benefits of Refractory Materials in High-Pressure Applications:
Examples of High-Pressure Applications Utilizing Refractories:
Pennekamp Middle East: Your Trusted Partner for High-Pressure Refractory Solutions
Pennekamp Middle East is a leading supplier of high-performance refractory materials specifically designed for demanding high-pressure applications. We offer a wide range of refractory products, each formulated with the optimal combination of strength, chemical stability, and thermal properties to meet your specific needs.
Contact Pennekamp Middle East today to discuss your high-pressure refractory requirements and discover how our solutions can help you achieve optimal performance, safety, and efficiency in your operations.