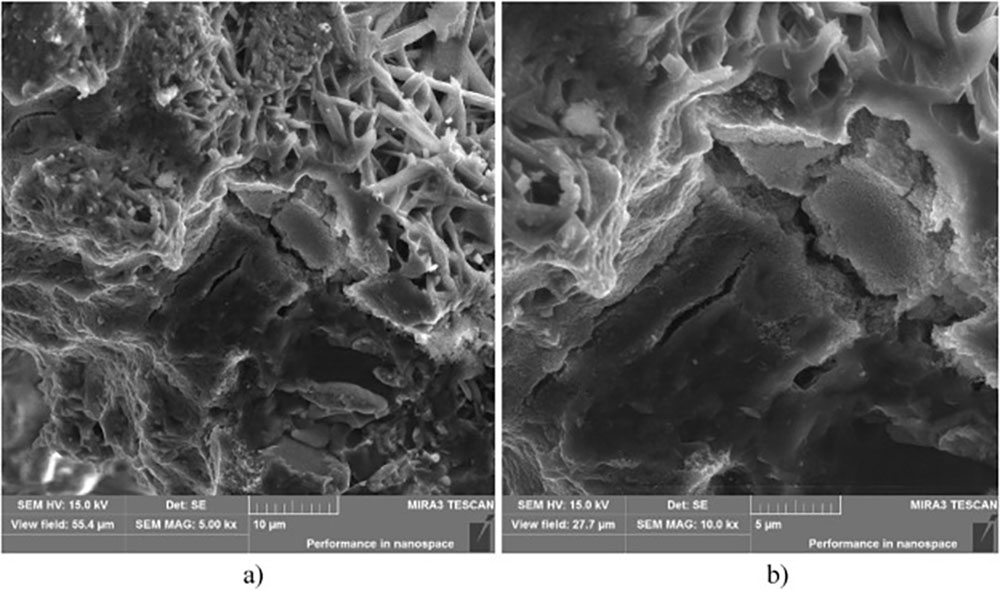
In high-temperature industrial applications, selecting the correct refractory material is essential to achieving durability, energy efficiency, and overall operational effectiveness. The performance of refractories is directly influenced by their chemical composition, which affects how they respond to heat, slag, and other challenging conditions within furnaces, kilns, and reactors.
Understanding the impact of these chemical elements helps industries choose the best materials for their unique needs, whether it’s a blast furnace in a steel plant or a rotary kiln in cement manufacturing. Here’s how the chemical composition of refractory materials affects their core properties:
High-temperature operations require materials that can withstand intense heat without degrading. The presence of elements like alumina, magnesia, and zirconia significantly enhances thermal resistance, while minimizing thermal conductivity ensures that furnaces maintain optimal temperatures with lower energy expenditure.
In industries like steel and glass production, where molten metals and aggressive slags are common, refractory materials must be chemically inert. The inclusion of compounds such as magnesia and chromium oxide in the composition enhances the material’s resistance to acidic and basic slags, reducing wear and extending service life.
The structure of a refractory material—whether dense or porous—depends largely on its chemical makeup. Additives like alumina and silicon carbide enhance mechanical strength and abrasion resistance, allowing refractories to withstand the mechanical stress of heavy-duty applications, like EAFs and ladles.
Sudden temperature fluctuations can cause refractory materials to crack and fail. Elements like silica and alumina help mitigate this by improving thermal shock resistance, ensuring that the material can endure rapid heating and cooling cycles without compromising structural integrity.
Optimizing Refractory Performance with the Right Composition
Selecting refractory materials with the correct chemical composition is crucial for minimizing downtime, reducing energy costs, and extending equipment lifespan. At Pennekamp Middle East, our extensive portfolio of refractory raw materials and finished products is designed with precision to meet the specific needs of various high-temperature industries. We provide custom solutions that help our clients enhance productivity and reduce maintenance costs.
Ready to optimize your operations with the right refractory materials? Connect with Pennekamp Middle East today and discover how our tailored solutions can improve your processes and efficiency, even in the most demanding conditions