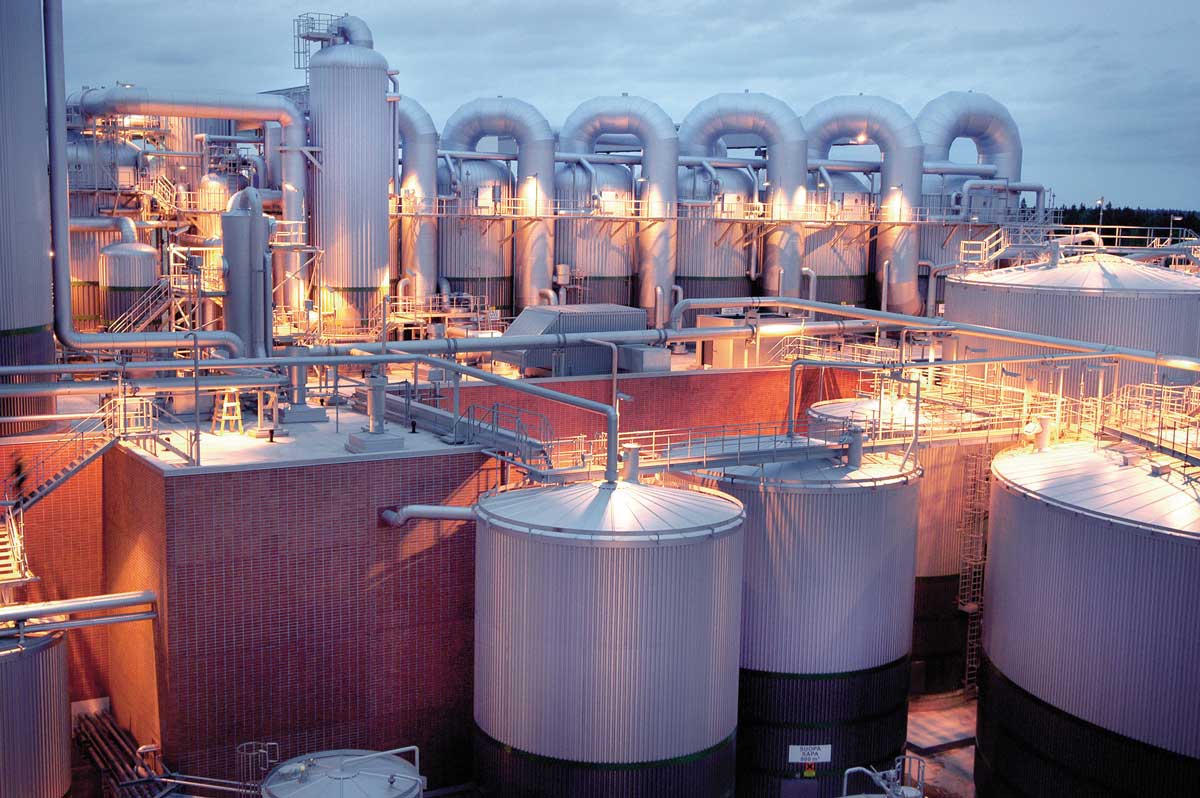
Chemical processing industries demand resilient solutions that can withstand harsh conditions and ensure optimal performance. In this pursuit, the significance of refractory materials cannot be overstated. Among the diverse options available, refractory plastics have gained prominence for their unique set of advantages in the realm of chemical processing.
Unparalleled Thermal Insulation:
One of the standout features of refractory plastics is their exceptional thermal insulation properties. These materials exhibit low thermal conductivity, effectively mitigating heat transfer and ensuring that equipment and structures maintain stability even in high-temperature environments. This characteristic not only enhances operational efficiency but also contributes to energy conservation, a crucial aspect in sustainable industrial practices.
Corrosion Resistance:
Chemical processing environments are notorious for their corrosive nature, posing a constant threat to equipment integrity. Refractory plastics, formulated with corrosion-resistant compounds, act as a robust defense against the corrosive effects of chemicals. This resistance not only prolongs the service life of the refractory materials but also safeguards the structural integrity of the processing equipment.
Lightweight and Flexible Installation:
Unlike traditional refractory materials, refractory plastics are known for their lightweight composition and flexibility during installation. This makes them an ideal choice for intricate structures and complex geometries within chemical processing units. The ease of handling and molding not only simplifies the installation process but also opens avenues for innovative design solutions tailored to specific operational needs.
Enhanced Thermal Shock Resistance:
Chemical processes often involve rapid temperature fluctuations, subjecting refractory materials to thermal shock. Refractory plastics excel in this regard, exhibiting superior resistance to thermal shock compared to conventional refractory materials. This characteristic minimizes the risk of material failure and ensures consistent performance, even in the face of abrupt temperature changes.
Cost-Efficient Maintenance:
The longevity and durability of refractory plastics contribute to cost-efficient maintenance over time. Their resistance to wear and tear, coupled with reduced downtime for repairs, translates into significant savings for chemical processing industries. This cost-effectiveness aligns with the broader goal of optimizing operational expenses without compromising on performance.
Incorporating refractory plastics into your chemical processing setup can revolutionize operational efficiency and longevity. Explore Pennekamp Middle East’s comprehensive range of refractory raw materials and finished products to discover innovative solutions tailored to your industry needs. Elevate your chemical processing capabilities with Pennekamp Middle East – where durability meets innovation. Contact us today to explore the possibilities.