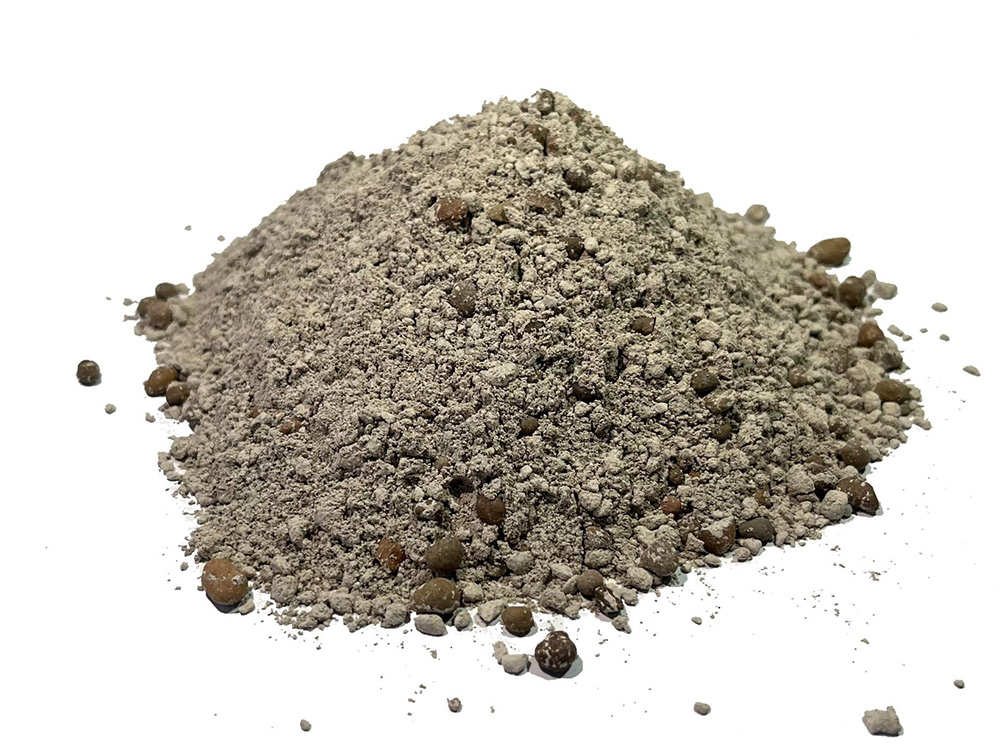
The Basic Oxygen Furnace (BOF) is a critical vessel in steel production, responsible for the rapid conversion of molten iron into steel. Operating under extreme conditions, the BOF relies heavily on robust and reliable refractories to withstand high temperatures, aggressive slags, and mechanical stresses. Magnesia-alumina based ramming mixes play a vital role in safeguarding the BOF’s integrity and optimizing its performance.
Understanding Magnesia-Alumina Ramming Mixes:
Magnesia-alumina ramming mixes are a popular choice for BOF applications due to their synergistic combination of properties offered by the two main components:
The specific ratio of magnesia to alumina within the mix can be tailored to optimize performance for different BOF zones. For instance, areas exposed to higher temperatures may benefit from mixes with a higher magnesia content, while areas requiring enhanced mechanical strength might utilize a higher alumina ratio.
Benefits of Magnesia-Alumina Ramming Mixes for BOF:
Applications of Magnesia-Alumina Ramming Mixes in BOF:
Magnesia-alumina ramming mixes are extensively used in various BOF applications, including:
Pennekamp Middle East: Your Trusted Supplier for High-Performance BOF Refractories
Pennekamp Middle East is a leading provider of high-quality magnesia-alumina based ramming mixes specifically designed for BOF applications. We offer a variety of formulations to cater to the diverse needs of different BOF zones and operational requirements. Our team of refractory experts can assist you in selecting the optimal ramming mix for your BOF and provide guidance on proper application techniques.
By incorporating magnesia-alumina ramming mixes into your BOF refractory strategy, you can ensure the vessel’s longevity, optimize operational efficiency, and achieve consistent high-quality steel production.