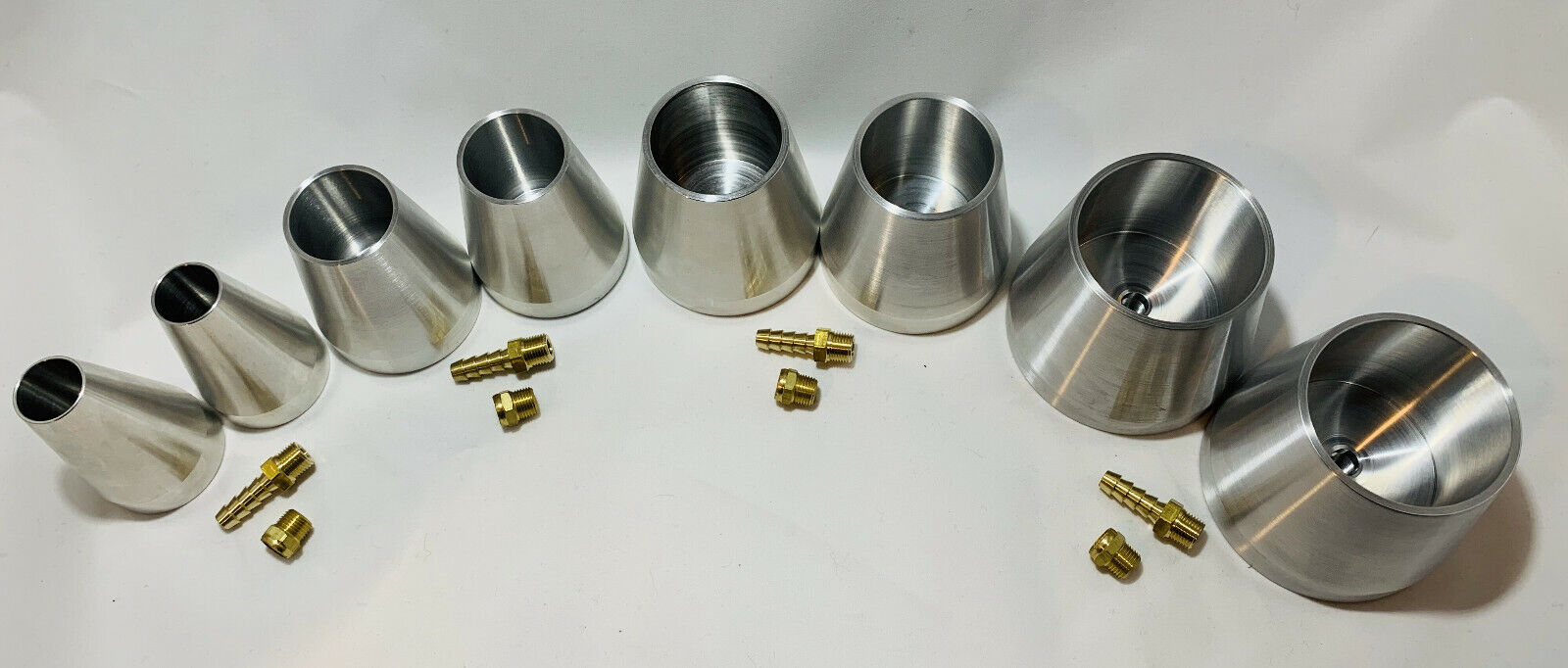
Steel production relies on precise control, and purging is essential for ensuring quality. This process uses inert gas to stir molten steel, improving temperature distribution, removing inclusions, and enhancing chemical reactions. Purging plugs, specifically purging plugs and porous plugs, are at the heart of this operation.
Purging Plugs: High-Heat Heroes
Installed at ladle bottoms, purging plugs allow inert gas injection into the molten steel. They endure extreme temperatures, chemical attack, and gas flow erosion. Careful design and robust materials are crucial for optimal performance and lifespan.
Two Types of Purging Plugs:
Choosing the Right Plug:
Selection depends on factors like steel grade, ladle size, and desired gas flow.
Benefits of Purging Plugs:
Porous Plugs: A Closer Look
Made from high-purity materials with controlled porosity, porous plugs allow gas to permeate throughout the plug structure for even gas distribution.
Advantages of Porous Plugs:
Considerations for Porous Plugs:
Optimizing Performance:
Conclusion:
Purging plugs, especially porous plugs and slit plugs, are essential for efficient steel production. By promoting effective stirring, they enhance steel quality and contribute to a successful steelmaking process.
For more information on purging plugs and how they can benefit your steel production, contact us today!