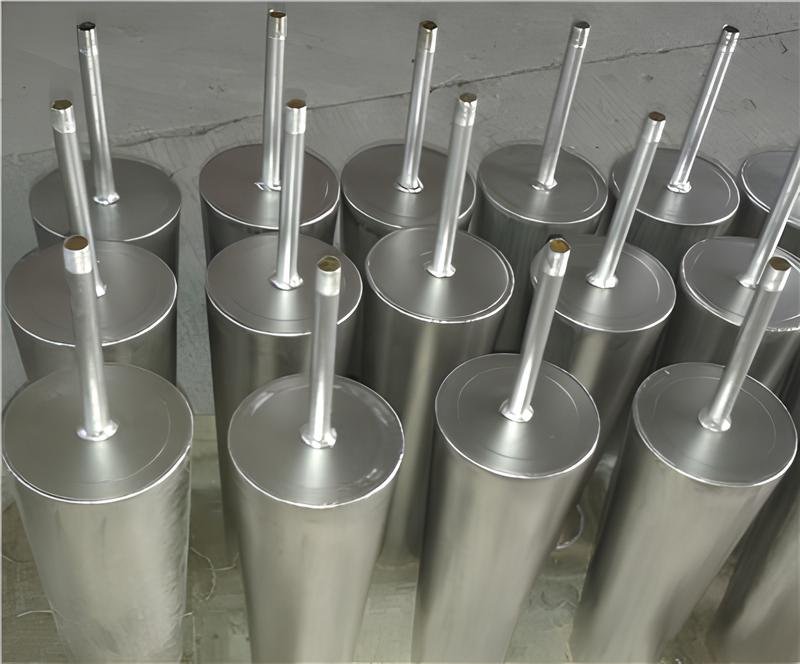
Introduction
In the steelmaking industry, maintaining control over the refining process is crucial for producing high-quality steel. One of the key components that facilitate this control is the purging plug, an often-overlooked yet vital part of the converter. This blog will explore the importance of purging plugs in steelmaking, their role in refining molten steel, and why they are indispensable for efficient and high-quality steel production.
What is a Purging Plug?
A purging plug is a refractory component installed at the bottom of the converter, designed to introduce gases, such as argon or nitrogen, into the molten steel during the refining process. This controlled gas flow helps to homogenize the molten steel, remove impurities, and improve the overall quality of the steel being produced.
The Role of Purging Plugs in Steelmaking
Benefits of Using Purging Plugs in Converters
Conclusion
Purging plugs are an essential component in the steelmaking process, offering numerous benefits that contribute to the production of high-quality steel. From enhancing the homogeneity of molten steel to improving process efficiency and reducing costs, purging plugs play a crucial role in modern steel production. At Pennekamp Middle East, we understand the importance of reliable and effective purging plug solutions, and we are committed to providing the highest quality refractory products to meet the demanding needs of the steelmaking industry.