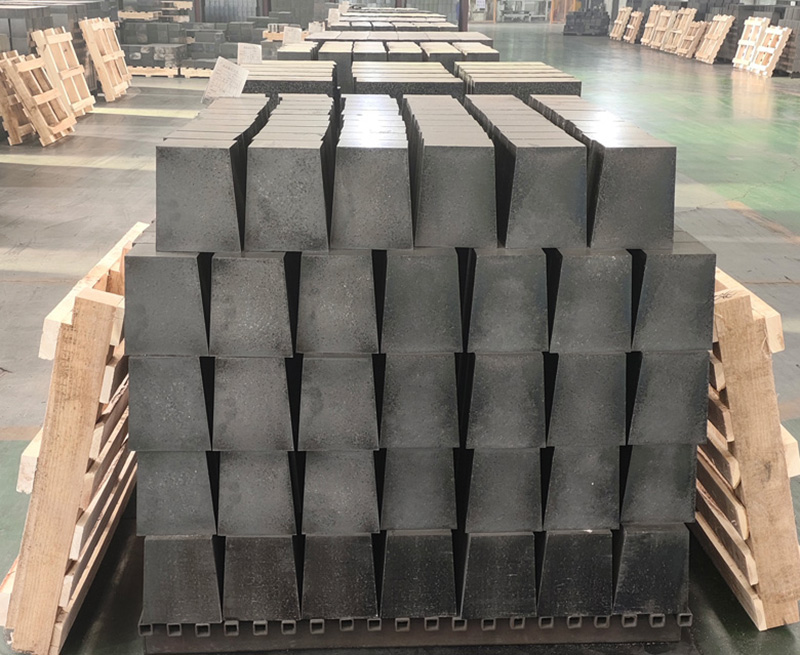
Ladle furnaces play a critical role in refining steel by adjusting temperature and chemistry after it’s produced in the blast furnace. However, the harsh conditions inside ladle furnaces, including high temperatures, slag exposure, and thermal shock, require durable and reliable refractory solutions. This is where MgO-C bricks shine, offering enhanced performance compared to other refractory types.
Key Advantages of MgO-C Bricks
How MgO-C Bricks Perform in Ladle Furnace Applications
Ladle furnaces operate at temperatures exceeding 1,600°C, making the selection of the right refractory material critical. MgO-C bricks offer outstanding performance in the following ways:
Partnering with Pennekamp Middle East for Superior MgO-C Bricks
At Pennekamp Middle East, we are committed to providing high-performance MgO-C bricks designed for ladle furnace applications. Our solutions are engineered to meet the specific demands of steel production environments and offer:
Conclusion
MgO-C bricks are indispensable for ladle furnaces, offering superior resistance to thermal shock, slag attack, and mechanical stress. By choosing Pennekamp Middle East’s advanced MgO-C bricks, steel manufacturers can extend the lifespan of their ladle furnaces, reduce maintenance costs, and improve overall production efficiency.
Reach out to Pennekamp Middle East today for more information on how our MgO-C bricks can enhance your ladle furnace operations.