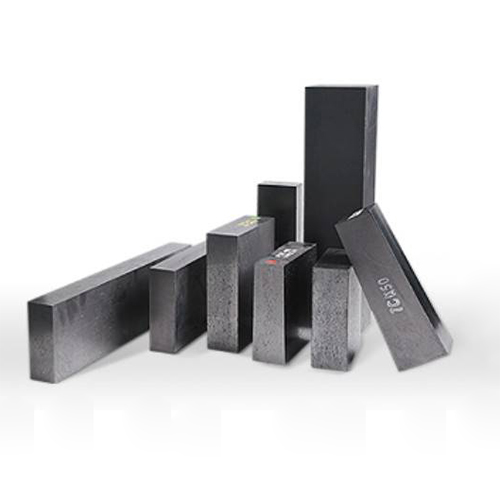
In the heart of electric arc furnace (EAF) steel production lies a crucial player: the MgO-C brick. These unassuming bricks, formed from magnesia (MgO) and carbon (C), are the workhorses lining the EAF walls, enduring extreme temperatures, harsh chemical environments, and intense mechanical wear. Understanding MgO-C bricks and their role in EAF operations is vital for optimizing steel production efficiency and product quality.
The Science Behind MgO-C Bricks:
MgO-C bricks leverage the complementary properties of magnesia and carbon. Magnesia offers exceptional thermal shock resistance and superior resistance to slag corrosion. Carbon, on the other hand, boasts high thermal conductivity and electrical conductivity, essential for efficient heat transfer within the furnace. The specific ratio of MgO to C in the brick is carefully chosen based on the specific zone within the EAF, as different zones demand varying properties.
Benefits of MgO-C Bricks in EAFs:
Types of MgO-C Bricks for Different EAF Zones:
The EAF environment varies significantly across different zones. To address these variations, MgO-C bricks are formulated with specific MgO to C ratios:
Optimizing EAF Performance with MgO-C Bricks:
Selecting the right MgO-C brick type for each EAF zone and maintaining proper installation practices are critical for optimal performance. Here are some key considerations:
Pennekamp Middle East: Your Partner in EAF Refractory Solutions
At Pennekamp Middle East, we are a leading provider of high-performance MgO-C bricks specifically designed for EAF applications. Our extensive product portfolio caters to all EAF zones, and our team of experts can guide you in selecting the optimal MgO-C brick solution for your specific needs. We are committed to providing exceptional quality, technical expertise, and reliable service to ensure your EAF operations run smoothly and efficiently.
Contact Pennekamp Middle East today to discuss your EAF refractory needs and discover how our high-quality MgO-C bricks can elevate your steel production process!