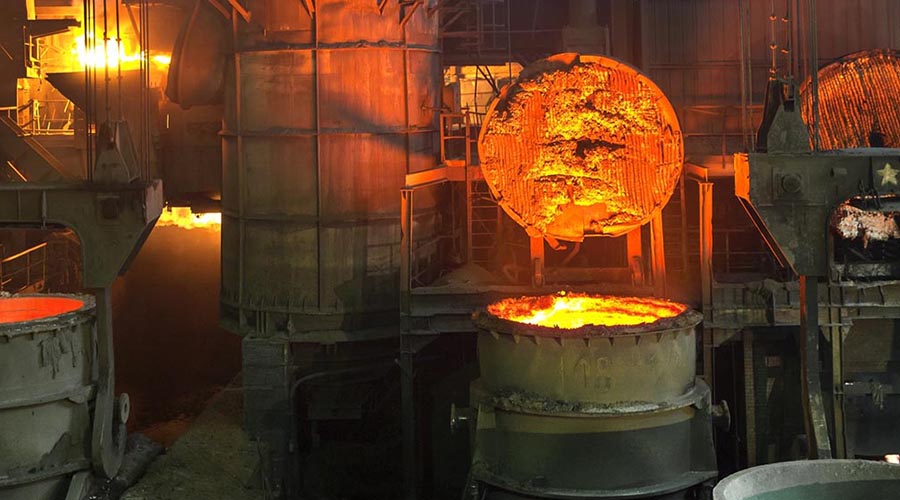
Introduction
Thermal conductivity is a fundamental property of refractory products that plays a crucial role in various high-temperature industrial processes. Whether in steelmaking, cement production, or any other application involving extreme heat, the ability of refractory materials to conduct or insulate heat effectively can significantly impact operational efficiency, energy consumption, and the longevity of the equipment. Optimizing thermal conductivity is therefore essential for achieving better performance and cost savings in industrial settings.
Understanding Thermal Conductivity in Refractories
Thermal conductivity refers to the ability of a material to transfer heat. In the context of refractories, it determines how heat moves through the material under high-temperature conditions. Materials with high thermal conductivity allow for quick heat transfer, which can be beneficial in certain applications where rapid heat dissipation is required. Conversely, materials with low thermal conductivity are used to insulate and retain heat, reducing energy loss and protecting surrounding structures.
Key Factors Influencing Thermal Conductivity
Strategies for Optimizing Thermal Conductivity
Conclusion
Optimizing the thermal conductivity of refractory products is a nuanced process that requires a deep understanding of material science and application requirements. By carefully selecting materials, adjusting manufacturing processes, and considering operational temperatures, it is possible to achieve the desired thermal performance, ultimately leading to more efficient and cost-effective industrial operations. At Pennekamp Middle East, we are committed to providing high-quality refractory materials tailored to meet the specific needs of our clients, ensuring optimal thermal conductivity and enhanced performance in every application.