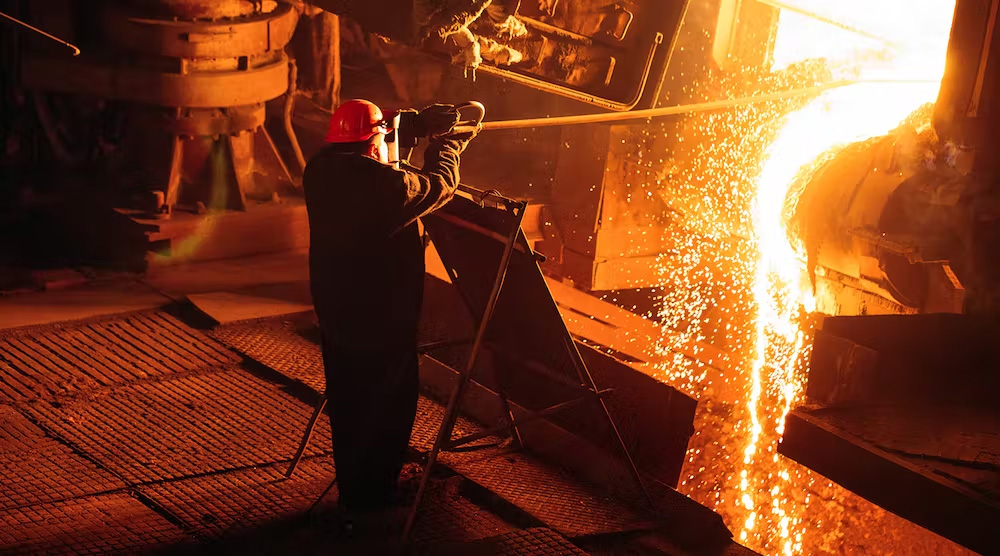
Refractory products play a crucial role in industries that operate under extreme temperatures, such as steelmaking, glass production, and petrochemical refining. One of the most significant challenges faced by these materials is erosion — the gradual wearing away of the material’s surface due to mechanical forces, thermal shock, and exposure to aggressive chemicals. Over time, erosion can lead to failure, increased maintenance costs, and reduced operational efficiency. Improving the erosion resistance of refractory products is essential for enhancing their durability and performance.
In this blog, we will explore key strategies to improve the erosion resistance of refractory products and how these approaches can extend their lifespan and effectiveness in high-stress environments.
Understanding Erosion in Refractory Products
Erosion in refractories occurs when solid particles, such as molten metal, slag, or abrasive materials, impact the surface of the refractory, causing the material to wear away. This process is accelerated by high temperatures, aggressive chemical exposure, and the mechanical stresses commonly encountered in industrial applications. As a result, refractories with poor erosion resistance can degrade quickly, leading to increased downtime and operational inefficiencies.
Strategies to Improve Erosion Resistance
- Material Composition Optimization
The composition of refractory materials plays a critical role in their erosion resistance. Magnesia-based refractories, Alumina, and Chromium Oxide are known for their high resistance to erosion, as they can withstand the abrasive forces and chemical exposure typically found in high-temperature processes.- Magnesia-alumina spinel is one example of a composite material that offers enhanced erosion resistance due to its improved toughness and wear resistance compared to traditional alumina or magnesia-based refractories.
- High-purity alumina is also highly resistant to abrasion and erosion, making it ideal for applications where mechanical wear is a concern.
- Use of Additives
Adding specific materials, such as graphite or zirconia, can improve the erosion resistance of refractory products. These additives increase the material’s ability to withstand abrasive forces and prevent excessive wear under high-stress conditions.- Zirconia (ZrO2)-based refractories are widely known for their enhanced erosion resistance, especially in extreme environments like those found in steelmaking and glass production.
- Carbon additives help reduce friction, improving the material’s resistance to abrasion and erosion.
- Increased Density and Porosity Control
Refractories with lower porosity are typically more resistant to erosion because they have fewer voids that can be worn away by abrasive particles. By increasing the density of the refractory, manufacturers can significantly improve the material’s ability to withstand erosion.- Higher density refractories tend to have better erosion resistance because they are less likely to allow for the penetration of abrasive materials into their structure.
- Controlled porosity can also help manage the refractory’s strength and thermal stability, ensuring it resists degradation even under heavy mechanical stress.
- Improved Bonding Matrix
The bonding matrix within the refractory material significantly affects its overall resistance to erosion. A stronger bond between the grains of the refractory material can prevent wear and tear. The use of advanced ceramic bonding agents can help increase the material’s resistance to mechanical erosion.- Chemical bonding agents can improve the refractory’s structural integrity and help it resist abrasion in high-stress environments.
- The use of reinforced bonding agents can enhance the overall durability of the refractory, ensuring longer service life in high-wear applications.
- Optimizing Manufacturing Processes
The manufacturing process plays a key role in enhancing the erosion resistance of refractory products. By improving firing and curing processes, manufacturers can produce refractories with superior mechanical properties.- Advanced firing techniques allow for the creation of refractories that are denser, stronger, and more resistant to both erosion and thermal shock.
- Heat treatment processes can optimize the internal structure of the refractory, making it more resilient to abrasive forces.
- Protective Coatings
Applying protective coatings to refractory products can significantly improve their resistance to erosion. These coatings form a barrier that protects the underlying material from abrasive forces and harsh chemicals.- Ceramic coatings can provide an additional layer of protection against erosion while maintaining the refractory’s high-temperature performance.
- Anti-abrasion coatings are specifically designed to enhance wear resistance in industrial environments, increasing the lifespan of refractory materials.
Pennekamp Middle East’s Erosion-Resistant Refractory Solutions
At Pennekamp Middle East, we provide a range of refractory products engineered to withstand the toughest conditions. Our advanced Magnesia, Alumina, and Spinel-based refractories are designed for superior erosion resistance, ensuring longevity and reliability in high-temperature applications. With years of experience and expertise, we offer tailored solutions to meet the unique challenges faced by industries such as steelmaking, glass production, and petrochemical refining.
Why Choose Pennekamp Middle East?
- Innovative Solutions: Our refractories are designed with cutting-edge technology to provide maximum erosion resistance.
- Durability and Reliability: We prioritize the longevity of our products, helping you reduce maintenance costs and improve operational efficiency.
- Tailored for Your Needs: We offer custom solutions to address the specific challenges of your high-temperature processes, ensuring optimal performance and protection.
Conclusion
Improving the erosion resistance of refractory products is essential for maintaining the performance and longevity of high-temperature equipment. By optimizing material composition, using additives, controlling porosity, enhancing bonding, and applying protective coatings, manufacturers can significantly increase the erosion resistance of their refractories. At Pennekamp Middle East, we provide advanced refractory solutions that meet the most demanding erosion resistance requirements, helping industries improve operational efficiency and reduce downtime.
Contact Pennekamp Middle East today to learn more about our erosion-resistant refractory products and how we can enhance the performance and longevity of your high-temperature applications.