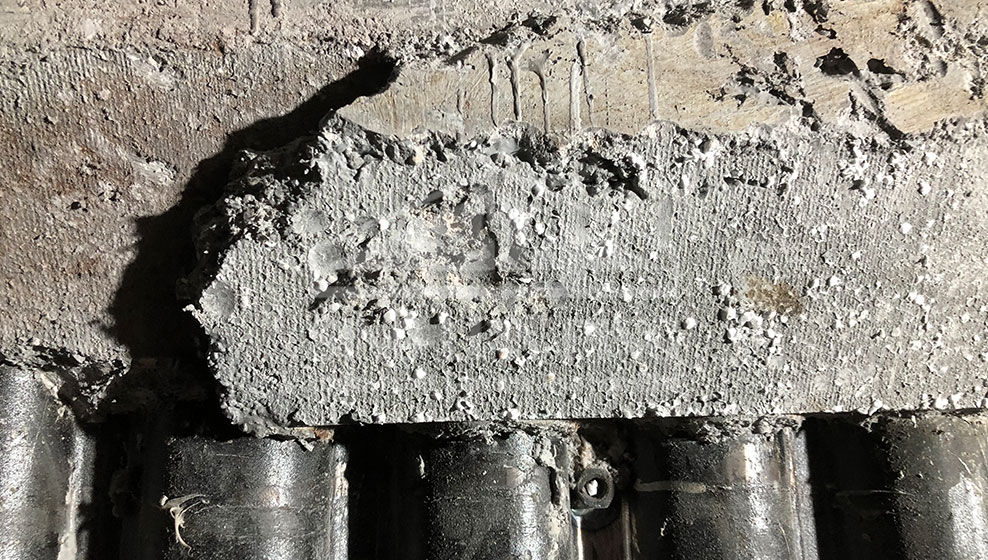
High-temperature applications require robust refractory products to withstand extreme heat and maintain optimal performance. However, despite their durability, refractory materials can face challenges and failures. Identifying and solving these issues promptly is crucial to prevent downtime and minimize costs. At Pennekamp Middle East, we are dedicated to providing industry-leading refractory raw materials and refractory finished products that deliver superior performance and longevity. In this blog post, we will explore common refractory product failures and provide actionable solutions to address them effectively.
One of the most common refractory product failures is thermal shock. This occurs when a refractory material is exposed to rapid temperature changes, leading to cracking, spalling, or complete failure. To identify thermal shock, look for visible cracks or signs of damage on the refractory surface. To mitigate this issue, selecting refractory materials with excellent thermal shock resistance is crucial. Additionally, implementing proper heating and cooling techniques, such as gradual temperature changes, can significantly reduce the risk of thermal shock.
Corrosion and erosion are frequent challenges faced by refractory products in high-temperature environments. Corrosion occurs when chemical reactions degrade the refractory material, while erosion happens due to the physical wear caused by abrasive substances. Signs of corrosion and erosion include thinning of the refractory lining, pitting, or surface roughness. Choosing refractory materials with high resistance to corrosive elements and abrasion is essential to mitigate these failures. Regular inspections, maintenance, and appropriate protective coatings can also help extend the lifespan of refractory products.
Spalling and cracking are significant concerns in refractory products, impacting their structural integrity and overall performance. Spalling refers to the breaking away of small pieces or chunks from the refractory surface, while cracking manifests as visible fissures or fractures. These failures can occur due to thermal stress, mechanical stress, or a combination of both. To prevent spalling and cracking, selecting refractory materials with high thermal stability, low thermal expansion, and good mechanical strength is vital. Proper installation techniques, including adequate curing and drying, can also minimize the risk of these failures.
Inadequate insulation in refractory products can result in heat loss, reduced energy efficiency, and increased operating costs. Poor insulation is often characterized by excessive heat transfer to the outer surface of the refractory, uneven temperature distribution, or higher-than-expected fuel consumption. Opting for refractory materials with excellent insulation properties, such as low thermal conductivity, is crucial to address this issue. Additionally, ensuring proper installation techniques, such as tight joints and effective insulation backing, can enhance insulation performance.
Identifying and solving common refractory product failures is essential for maintaining efficient and reliable high-temperature operations. By understanding the signs and causes of thermal shock, corrosion, erosion, spalling, cracking, and poor insulation, you can take proactive measures to mitigate these challenges. At Pennekamp Middle East, we offer a comprehensive range of refractory raw materials and refractory finished products that are specifically designed to withstand extreme heat and combat these failures effectively.
Are you experiencing refractory product failures and seeking reliable solutions to keep your operations running smoothly? Visit Pennekamp Middle East today to explore our comprehensive range of refractory raw materials and finished products. Our team of experts is ready to assist you in identifying and resolving any refractory challenges you may encounter. Contact us now and optimize the performance and longevity of your high-temperature processes.