High-temperature processes are essential in various industries, including steel production, cement manufacturing, petrochemical refining, and glass production. These industries rely on equipment such as furnaces, kilns, reactors, and incinerators, which are exposed to extreme heat, corrosive chemicals, and mechanical stresses. Refractory materials are critical in ensuring these high-temperature operations run efficiently and safely.
In this blog, we explore how advanced refractory materials are helping industries meet the challenges posed by high-temperature processes and why their role is more vital than ever.
The Role of Refractory Materials in High-Temperature Processes
Refractory materials are designed to withstand high temperatures, thermal shocks, and chemical exposure while maintaining their structural integrity. These materials are used as linings, coatings, or insulators for high-temperature equipment, protecting both the equipment and the processes taking place inside.
Key Challenges of High-Temperature Processes
- Extreme Heat Resistance: High-temperature environments often exceed 1,000°C, and in some cases, can reach up to 3,000°C, as seen in steelmaking or glass furnaces. Materials must withstand these intense temperatures without breaking down or losing strength.
- Thermal Shock and Cycling: Many industrial processes involve rapid temperature fluctuations, which can cause materials to crack or degrade if they are not resistant to thermal shock. This can lead to equipment failure, unplanned downtime, and higher operational costs.
- Chemical Corrosion: High-temperature processes expose materials to molten metals, slags, gases, and other aggressive chemicals that can cause corrosion or erosion over time. Refractory materials must be chemically stable to protect equipment and ensure safe, uninterrupted operations.
- Mechanical Stress: Refractory linings in high-temperature equipment are subject to mechanical stress from both the weight of the molten materials and the movement of machinery. These stresses can cause wear and tear, reducing the lifespan of the equipment.
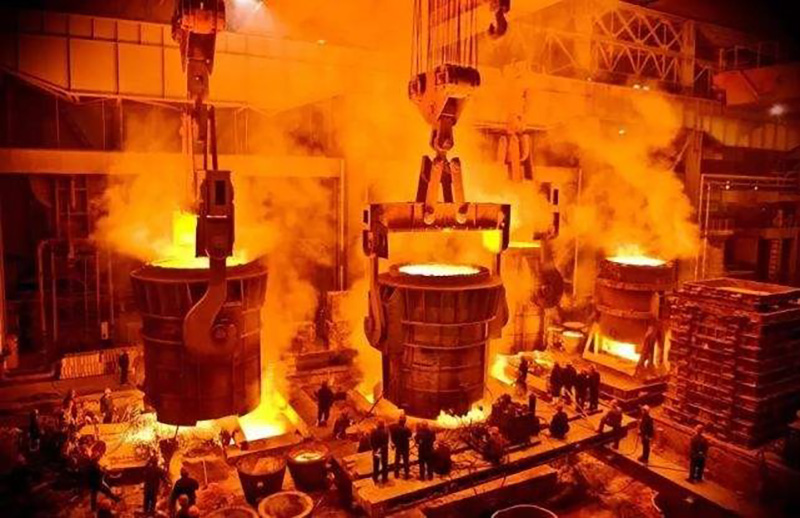
How Refractory Materials Meet These Challenges
- High-Temperature Resistance: Advanced refractory materials, such as Fused Mullite, Fused Alumina, and Magnesite, offer excellent thermal stability, allowing them to withstand extreme heat without softening or degrading. These materials help maintain the efficiency and safety of high-temperature operations, ensuring that the equipment remains in optimal working condition.
- Thermal Shock Resistance: Refractory materials like Silicon Carbide and Magnesia Chrome are designed to resist thermal shock, meaning they can handle rapid changes in temperature without cracking. This feature is essential in industries such as steelmaking, where furnaces are exposed to sudden heating and cooling cycles.
- Chemical Resistance: High-performance refractory materials are engineered to be chemically inert or resistant to molten metals, slags, and other aggressive chemicals. Materials like Caustic Calcined Magnesite and Chromium Oxide provide excellent protection against chemical corrosion, extending the life of high-temperature equipment.
- Durability and Strength: Refractories are designed to be durable and mechanically strong. Materials like Sintered Mullite and Magnesia Carbon offer high load-bearing capacity and resistance to erosion, ensuring that refractory linings can endure mechanical stresses and last longer.
Pennekamp Middle East’s Advanced Refractory Solutions
At Pennekamp Middle East, we provide a wide range of advanced refractory materials that meet the demanding requirements of high-temperature processes. Our products are engineered to provide excellent thermal resistance, durability, and chemical stability, ensuring your operations run smoothly and safely.
Why Choose Pennekamp Middle East?
- Customized Solutions: We offer tailored refractory materials designed to meet the specific challenges of your high-temperature processes.
- Enhanced Performance: Our materials are designed for superior thermal shock resistance, chemical stability, and mechanical strength, helping you achieve optimal performance.
- Proven Reliability: With years of experience and expertise, Pennekamp Middle East provides reliable, high-quality refractory solutions for industries around the world.
Conclusion
Refractory materials play an essential role in high-temperature processes by providing the heat resistance, thermal shock protection, chemical stability, and mechanical strength needed to ensure safe and efficient operations. As industries face increasing demands for performance and sustainability, the role of advanced refractories becomes more crucial in meeting these challenges.
At Pennekamp Middle East, we offer premium-quality refractory solutions designed to withstand the harshest conditions, providing long-lasting performance and efficiency for your high-temperature applications.
Contact Pennekamp Middle East today to learn more about how our advanced refractory materials can help meet the challenges of your high-temperature processes.