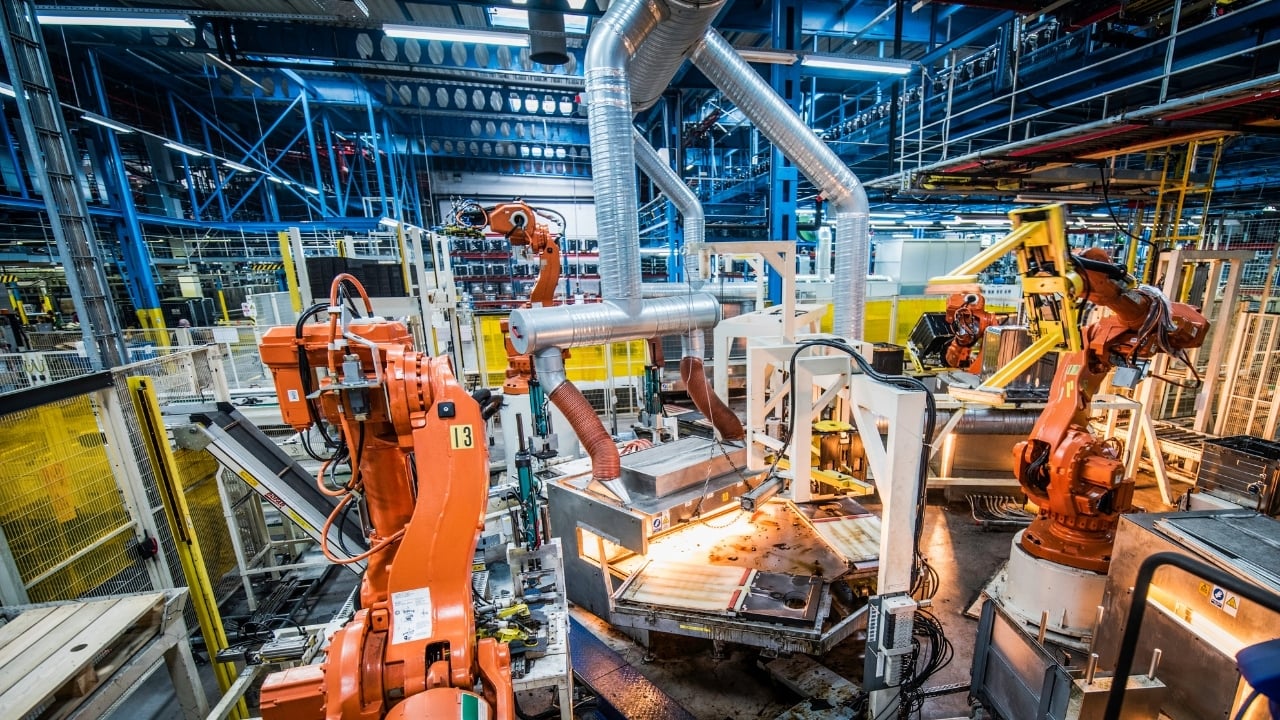
Introduction
The steel manufacturing industry is undergoing significant transformations driven by advancements in technology and a growing emphasis on efficiency and sustainability. Refractory materials, essential for withstanding the extreme conditions in steel production, are at the forefront of these innovations. As steelmakers strive to improve performance and reduce environmental impact, refractory innovations are playing a pivotal role in shaping the future of steel manufacturing. This blog explores the latest developments in refractory materials and technologies and their impact on the steel industry.
Advancements in Refractory Materials
Technological Innovations in Refractory Applications
Impact on Steel Manufacturing
Conclusion
Refractory innovations are playing a crucial role in shaping the future of steel manufacturing, driving improvements in efficiency, sustainability, and performance. The development of high-performance materials, eco-friendly solutions, and advanced technologies is transforming the steel industry, enabling manufacturers to meet the demands of a changing world. At Pennekamp Middle East, we are committed to staying at the forefront of refractory innovations, providing cutting-edge solutions that enhance the performance and sustainability of steelmaking operations.