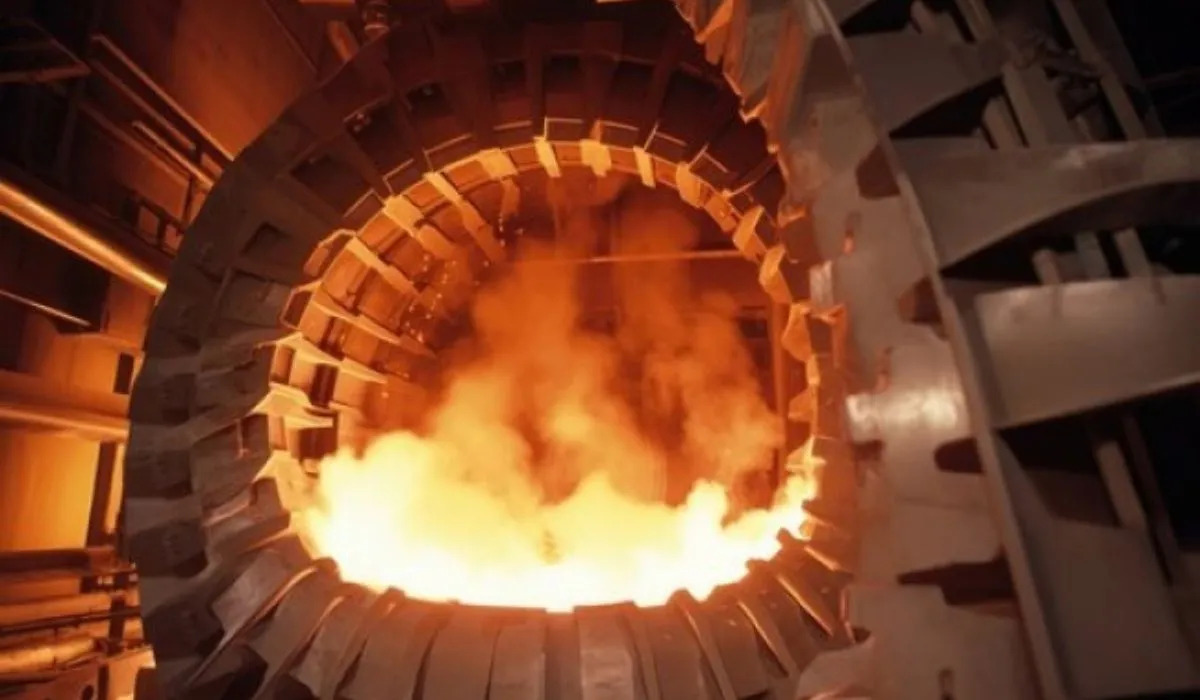
Introduction
Refractory materials are critical in industrial processes that involve high temperatures, corrosive environments, and extreme conditions. Over the years, these materials have evolved significantly to meet the changing demands of modern industries. From traditional clay-based refractories to cutting-edge composites, the evolution of refractory materials reflects advances in technology and a deeper understanding of material science. This blog will explore the key developments in refractory materials, their current innovations, and their impact on industrial performance.
Historical Overview of Refractory Materials
Historically, refractory materials were primarily composed of natural minerals such as fireclay and silica. These early refractories were used in basic applications like furnace linings and kilns, where their primary role was to withstand high temperatures. As industrial processes became more complex and demanding, the limitations of traditional refractories became apparent, leading to the development of more advanced materials.
Key Developments in Refractory Materials
Current Innovations in Refractory Materials
Impact on Industrial Performance
The evolution of refractory materials has had a profound impact on industrial performance, offering several benefits:
Conclusion
The evolution of refractory materials reflects the ongoing advancements in material science and technology. From their early origins to the latest innovations, refractories have continuously adapted to meet the demands of modern industries. As we look to the future, ongoing research and development will likely bring even more advanced and sustainable refractory solutions, further enhancing industrial efficiency and performance. At Pennekamp Middle East, we are committed to staying at the forefront of refractory technology, providing our clients with the most advanced materials to meet their evolving needs.