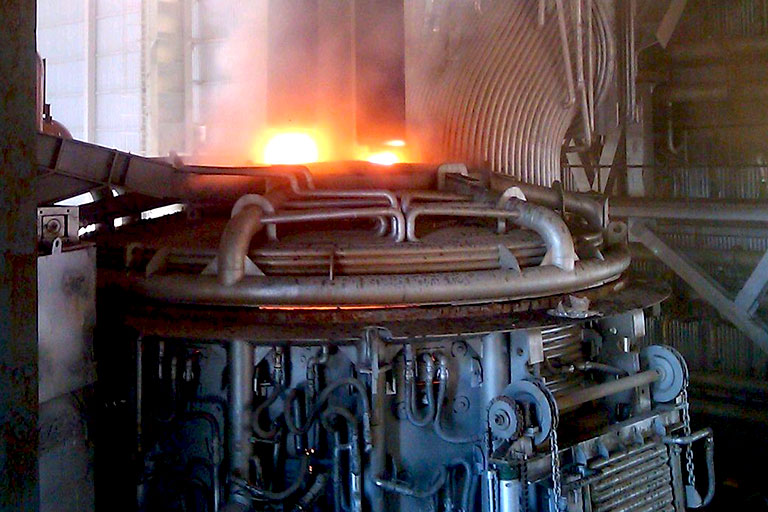
Introduction
Electric Arc Furnaces (EAFs) are central to modern steel production, providing a method for melting scrap metal and producing high-quality steel. One of the crucial components in the efficient operation of EAFs is the taphole filling mass, used to seal the taphole during the steel tapping process. This blog delves into the importance of EBT (Electric Arc Furnace) taphole filling mass, its properties, and the role it plays in maintaining the efficiency and reliability of steel production.
What Is EBT Taphole Filling Mass?
EBT taphole filling mass is a specialized refractory material used to seal the taphole in an electric arc furnace. The taphole, which is the outlet through which molten steel is tapped from the furnace, requires a robust and durable filling material to prevent leakage and maintain proper flow control. The filling mass is designed to withstand the extreme temperatures and chemical conditions present in the EAF environment.
Key Properties of EBT Taphole Filling Mass
Benefits of Using EBT Taphole Filling Mass
Applications of EBT Taphole Filling Mass
Conclusion
EBT taphole filling mass is a critical component in the steel production process, providing essential sealing and protection for the taphole in electric arc furnaces. With its high temperature resistance, thermal shock resistance, chemical resistance, and mechanical strength, this refractory material contributes to the efficiency, safety, and cost-effectiveness of steelmaking operations. At Pennekamp Middle East, we are dedicated to providing high-quality EBT taphole filling mass that meets the demanding requirements of modern steel production, ensuring optimal performance and reliability in every application.