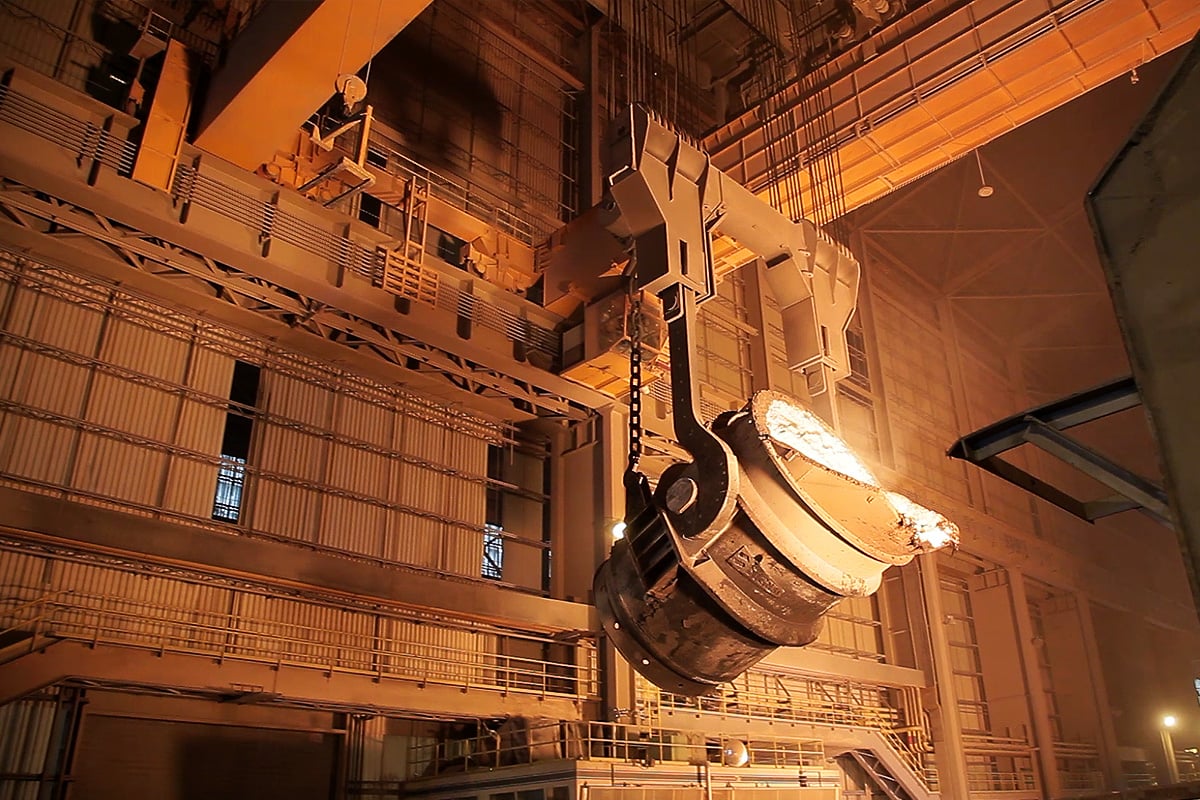
Introduction
In steelmaking and foundry operations, charge ladles play a critical role in the handling and transportation of molten metal from furnaces to casting molds. The effectiveness and longevity of these ladles depend significantly on the quality of the refractory materials used to line them. Castables, a type of refractory material applied in a liquid or paste form, are crucial for ensuring the efficient and reliable operation of charge ladles. This blog examines the properties and advantages of castables for charge ladles and their role in enhancing metal handling processes.
What Are Castables for Charge Ladles?
Castables are refractory materials made from a blend of high-performance aggregates, binders, and additives. They are mixed with water to form a pourable or pumpable paste, which is then cast into the desired shape and allowed to cure. Castables used for charge ladles are specifically formulated to withstand the extreme conditions encountered during metal handling, including high temperatures, mechanical stresses, and chemical exposure.
Key Properties of Castables for Charge Ladles
Benefits of Using Castables for Charge Ladles
Applications of Castables for Charge Ladles
Conclusion
Castables for charge ladles are essential for ensuring efficient and reliable metal handling in steelmaking and foundry operations. With their high thermal stability, thermal shock resistance, chemical resistance, and mechanical strength, castables contribute to the optimal performance and extended lifespan of ladle linings. At Pennekamp Middle East, we are committed to providing advanced castable solutions tailored to meet the rigorous demands of metal handling applications, ensuring superior performance and durability in every operation.