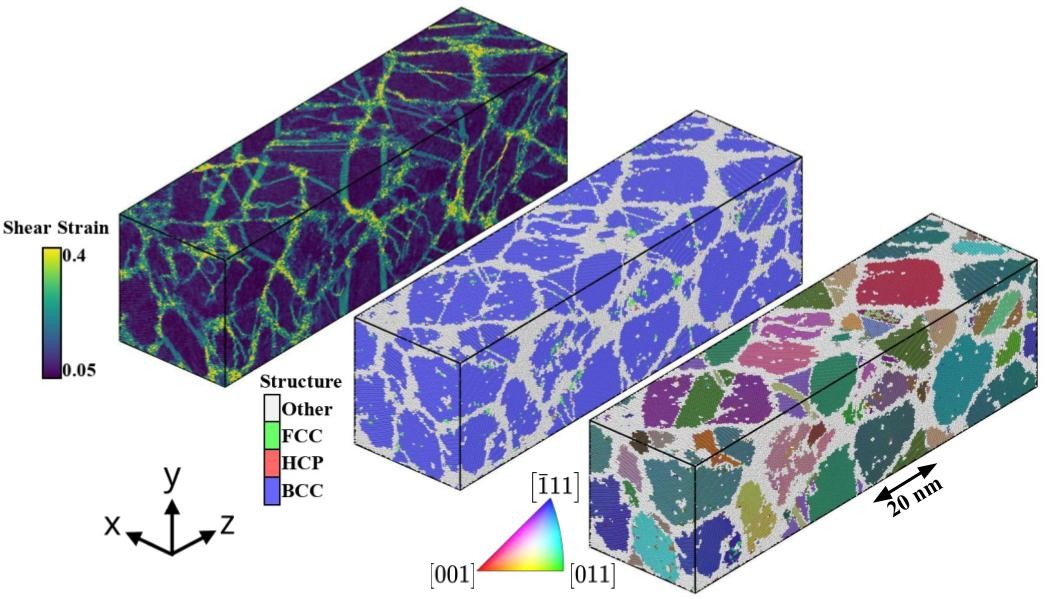
Why Grain Size Matters in Refractories
In the world of high-temperature industrial processes—such as steelmaking, glass production, or cement manufacturing—refractory linings are the unsung heroes. These linings protect furnaces and vessels from intense heat and wear. But not all refractories are created equal. One of the most critical and often overlooked aspects of their performance is grain size distribution.
Grain size refers to the diameter of individual particles used in the refractory mix—ranging from coarse aggregates to fine powders. The balance of these sizes within a formulation is called the distribution curve, and it directly affects the structure, porosity, and strength of the final product.
How Grain Size Distribution Affects Performance
Grain Size Optimization at Pennekamp Middle East
At Pennekamp Middle East, we understand that grain size isn’t just a number—it’s a performance factor. That’s why our raw materials, including fused magnesia, alumina, silica, and zircon, go through strict grading and quality control processes. Whether you’re sourcing monolithic refractories, refractory mortars, or castables, we ensure the right blend of grain sizes for your specific industrial use.
Our technical team also supports customers with tailored grain size distributions depending on the application—be it steel ladles, tundishes, rotary kilns, or iron mixers.
Looking for Consistent Refractory Performance? Start with the Right Grain Size.
Partner with Pennekamp Middle East to get high-performance refractory raw materials with optimized grain size distributions. Contact us today to discuss your material needs and improve your furnace reliability.