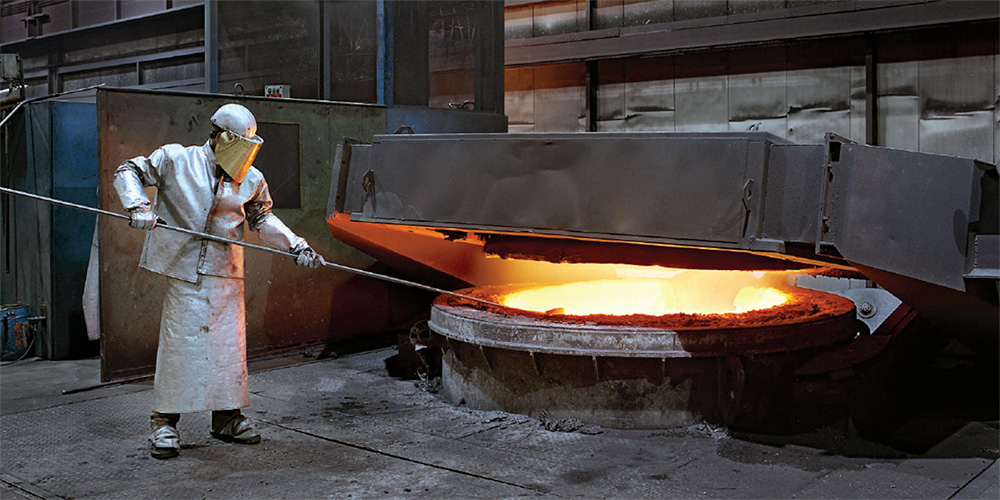
In high-temperature industrial processes, refractories are vital for ensuring the efficiency and longevity of equipment. However, achieving optimal performance from these materials often requires more than just the right base composition. Additives play a critical role in fine-tuning the properties of refractories, improving their ability to withstand extreme conditions, resist chemical attack, and maintain structural integrity over time. Understanding the role of additives in refractory materials is essential for optimizing their performance and ensuring the reliability of industrial operations.
What Are Additives in Refractories?
Additives are substances incorporated into refractory materials during their manufacturing process to modify or enhance specific properties. These additives can be inorganic compounds, such as oxides, carbides, or nitrides, or organic materials, such as binders and plasticizers. The goal is to improve characteristics like thermal conductivity, resistance to wear and tear, chemical stability, and overall durability.
Key Benefits of Additives in Refractory Materials
- Improved Thermal Stability: Many additives help refractories maintain their structural integrity under high temperatures. For example, alumina-based additives can increase the material’s resistance to thermal shock, allowing it to endure rapid temperature fluctuations without cracking or degrading.
- Enhanced Chemical Resistance: Refractories are often exposed to aggressive chemicals, including molten metals, slags, and acids. Additives like zirconium oxide or silicon carbide can enhance the material’s ability to resist chemical attack, extending the lifespan of refractories and minimizing downtime for repairs or replacements.
- Reduced Wear and Tear: Certain additives, such as silicon carbide or graphite, improve the mechanical strength of refractories, making them more resistant to abrasion, erosion, and wear. This is particularly valuable in applications where refractories come into direct contact with high-velocity gases, molten metals, or other abrasive materials.
- Better Mechanical Strength: Additives can also improve the mechanical properties of refractories, such as their load-bearing capacity and resistance to deformation under pressure. This is crucial for ensuring the stability of refractory linings in furnaces, kilns, and reactors, where heavy loads and mechanical stresses are common.
- Tailored Performance for Specific Applications: By selecting the right combination of additives, manufacturers can design refractories that are precisely suited to specific industrial processes. Whether it’s improving the refractoriness of a material for a high-temperature steel-making process or enhancing its insulating properties for furnace linings, additives allow for greater customization of refractory materials.
Common Additives Used in Refractories
- Silicon Carbide (SiC): Enhances resistance to thermal shock and chemical attack, while also improving strength and wear resistance.
- Zirconia (ZrO2): Increases resistance to high-temperature corrosion and is especially useful in environments with molten metals or slags.
- Magnesium Oxide (MgO): Improves the refractory’s resistance to basic slags and enhances its thermal conductivity, making it ideal for certain furnace linings.
- Graphite: Offers high thermal conductivity, reduced friction, and improved resistance to wear, making it useful in applications like ladle linings.
- Alumina (Al2O3): Adds thermal shock resistance and helps increase the refractoriness of the material, making it ideal for high-temperature applications.
Pennekamp Middle East’s Advanced Refractory Solutions with Additives
At Pennekamp Middle East, we leverage the power of specialized additives to create high-performance refractory materials for industries operating under extreme conditions. By integrating carefully selected additives, we enhance the thermal, mechanical, and chemical properties of our refractories, ensuring that they meet the specific needs of each application.
Benefits of Choosing Pennekamp Middle East:
- Customized Solutions: We tailor our refractory products with the right additives to meet the unique requirements of your high-temperature applications.
- Enhanced Durability: Our additives improve the performance of refractories, ensuring longer service life and reduced maintenance costs.
- Superior Performance: Whether it’s for thermal shock resistance, chemical attack, or mechanical strength, our refractory solutions are engineered to deliver optimal performance in even the most demanding environments.
Conclusion
Additives are essential in enhancing the properties of refractory materials, ensuring that they can withstand the extreme conditions of high-temperature industrial processes. By incorporating the right additives, we can improve thermal stability, chemical resistance, wear resistance, and overall durability, optimizing the performance of refractories in a wide range of applications.
At Pennekamp Middle East, we offer advanced refractory solutions with the right additives to meet your specific operational needs. Our team of experts can help you select the most suitable materials to enhance the performance and longevity of your industrial equipment.
Contact Pennekamp Middle East today to learn more about our additive-enhanced refractory solutions and how they can optimize your high-temperature operations.