Foundries operate at extreme temperatures where metals like steel, iron, aluminum, and copper are melted, cast, and treated. These processes require lining systems that can withstand heat, resist corrosion from molten metals and slag, and maintain structural integrity. That’s where refractory products come in.
From furnace linings and ladles to runners, tundishes, and crucibles, refractories are the hidden champions of foundry reliability. Without them, frequent shutdowns, material contamination, and excessive energy use would be the norm.
Core Functions of Refractory Products in Foundries
- Thermal Resistance:
Refractories act as a heat barrier, maintaining temperature uniformity inside the furnace and minimizing heat loss. This improves thermal efficiency and energy conservation—critical for both environmental impact and cost savings.
- Mechanical Strength:
Foundry environments are rough. Refractories must endure abrasion, mechanical impact, and rapid heating/cooling cycles. High-quality materials like magnesia, alumina, and silica help withstand this constant stress.
- Chemical Protection:
Molten metals and fluxes are aggressive. Without chemical-resistant refractory linings, equipment would corrode rapidly. Customized refractory mixes are designed to resist chemical reactions, oxidation, and slag attacks.
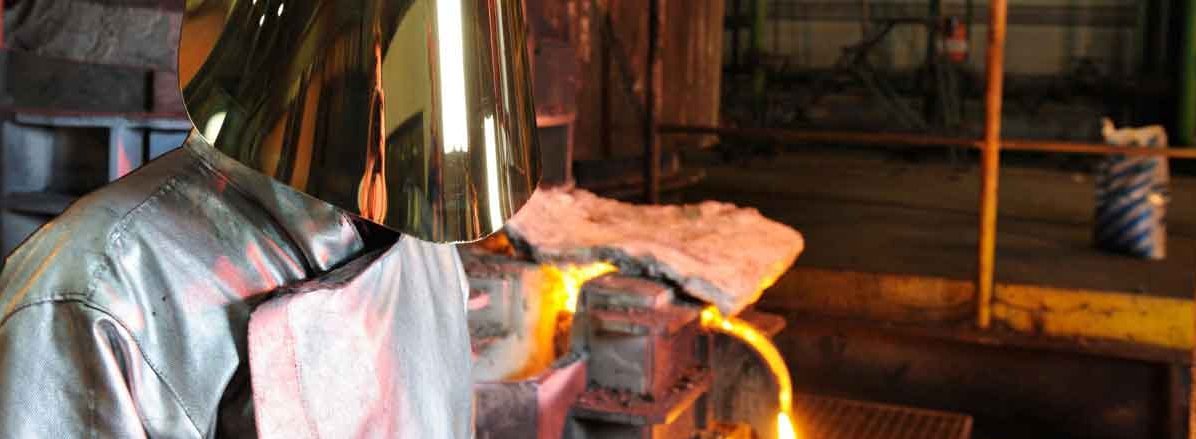
Key Refractory Applications in Foundries
- Melting Furnaces (Coreless and Channel Induction Furnaces):
Use high-alumina and silica-based linings to withstand metal contact and high thermal loads.
- Ladles and Transfer Equipment:
Require wear-resistant and thermally stable refractories, such as magnesia-carbon bricks and insulating castables.
- Tundishes and Casting Channels:
Often lined with low-cement castables and pre-cast shapes for smooth metal flow and reduced turbulence.
- Crucibles and Molds:
Specialized refractories that combine thermal insulation with resistance to erosion and thermal shock.
Choosing the Right Refractory: What Foundries Should Consider
Every foundry has unique requirements based on:
- Metal type (ferrous or non-ferrous)
- Melting temperatures
- Cycle times and thermal shocks
- Slag and chemical exposure
- Installation and maintenance capabilities
Partnering with a knowledgeable supplier like Pennekamp Middle East ensures you’re using the right materials for the job. We provide tailored refractory solutions backed by technical support, helping foundries boost efficiency and reduce downtime.
Sourcing and Quality Control at Pennekamp Middle East
As a trusted supplier of refractory raw materials and finished products, we ensure:
- Consistent sourcing of high-purity magnesia, alumina, silica, and specialty additives
- Strict quality testing for particle size, purity, thermal behavior, and mechanical strength
- Reliable global supply chains that reduce lead times and keep your operations moving
We don’t just deliver materials—we deliver performance.
Trends Shaping the Future of Foundry Refractories
- Precast and prefired shapes to reduce installation time and improve consistency
- Energy-efficient formulations that lower furnace heat loss
- Eco-friendly binders and recycled materials for sustainable casting
- AI-based monitoring to predict refractory wear and optimize maintenance
Modern foundries need modern solutions, and refractories are evolving to meet these challenges head-on.
Foundries can’t operate without dependable refractory materials. They’re the unsung heroes that keep heat in, wear out slower, and protect every step of the metal casting process.
Looking for expert guidance and reliable materials for your foundry? Connect with Pennekamp Middle East—your partner for premium refractory solutions built for modern metalcasting.