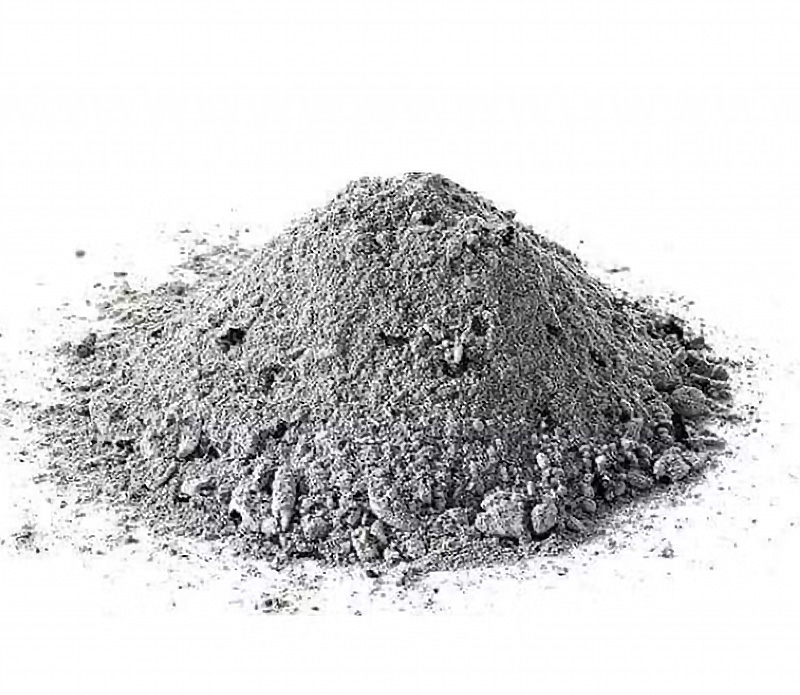
Charge ladles are an integral part of the steelmaking process, used to transport molten steel from the furnace to the refining vessel or casting machine. Due to the extreme temperatures and aggressive chemical conditions, the refractory lining inside charge ladles is subjected to constant wear. Protecting these linings is essential for maintaining the ladle’s functionality and extending its service life.
One of the most effective solutions for preserving the integrity of charge ladles is the use of hot spray mixes—specialized refractory materials designed for on-site application.
What Is Hot Spray Mix for Charge Ladle?
Hot spray mix is a refractory material applied to the interior lining of charge ladles using a spray technique. This process involves applying a high-quality, pre-mixed material while the ladle is still hot, allowing the material to bond directly to the lining, forming a durable, protective layer.
Benefits of Using Hot Spray Mix for Charge Ladles
- Enhanced Durability:
Hot spray mixes are specifically designed to withstand high temperatures and resist erosion caused by the repeated thermal cycles inside charge ladles. This results in longer service life and less frequent relining. - Improved Thermal Insulation:
The refractory properties of the hot spray mix help to reduce heat loss from the molten steel, improving thermal efficiency and reducing energy consumption. - Slag Resistance:
Hot spray mixes create a strong barrier against slag and molten steel, preventing damage to the ladle lining and ensuring better operational reliability. - Reduced Downtime:
The ability to apply the hot spray mix during operation without needing to cool the ladle reduces downtime, increasing productivity and minimizing maintenance costs. - Customizable Solutions:
Pennekamp Middle East offers tailored hot spray mixes designed to meet the specific needs of your charge ladles. Whether it’s for improving wear resistance or enhancing slag resistance, our solutions are built to perform under the harshest conditions.
How Hot Spray Mix Improves Charge Ladle Performance
Charge ladles operate under extreme conditions, with temperatures often exceeding 1,500°C. By using hot spray mixes, the internal lining of the ladle is protected from:
- Thermal Cycling: Hot spray mixes maintain their structure despite rapid heating and cooling, reducing wear and cracks.
- Chemical Attacks: The material is designed to resist the corrosive nature of slag and molten metal, ensuring the integrity of the ladle lining.
- Mechanical Stress: The refractory bond provided by hot spray mixes reinforces the ladle, enhancing its resistance to mechanical impact during handling and transportation.
Partnering with Pennekamp Middle East for Hot Spray Mix Solutions
At Pennekamp Middle East, we specialize in providing high-performance hot spray mixes for charge ladles. Our solutions are crafted to meet the most demanding requirements of steel manufacturing and offer:
- Customized Formulations: Tailored hot spray mixes to address your specific operational challenges.
- Expert Guidance: Technical support for efficient application and maintenance procedures.
- Proven Results: Our products are trusted by steel manufacturers worldwide for their durability and effectiveness.
Conclusion
Hot spray mixes for charge ladles offer a cost-effective and efficient solution for maintaining ladle linings in steel production. By using these advanced refractory materials, manufacturers can extend the lifespan of their charge ladles, improve operational efficiency, and reduce downtime.
Contact Pennekamp Middle East today to learn more about our high-quality hot spray mixes for charge ladles and how they can benefit your steelmaking operations.