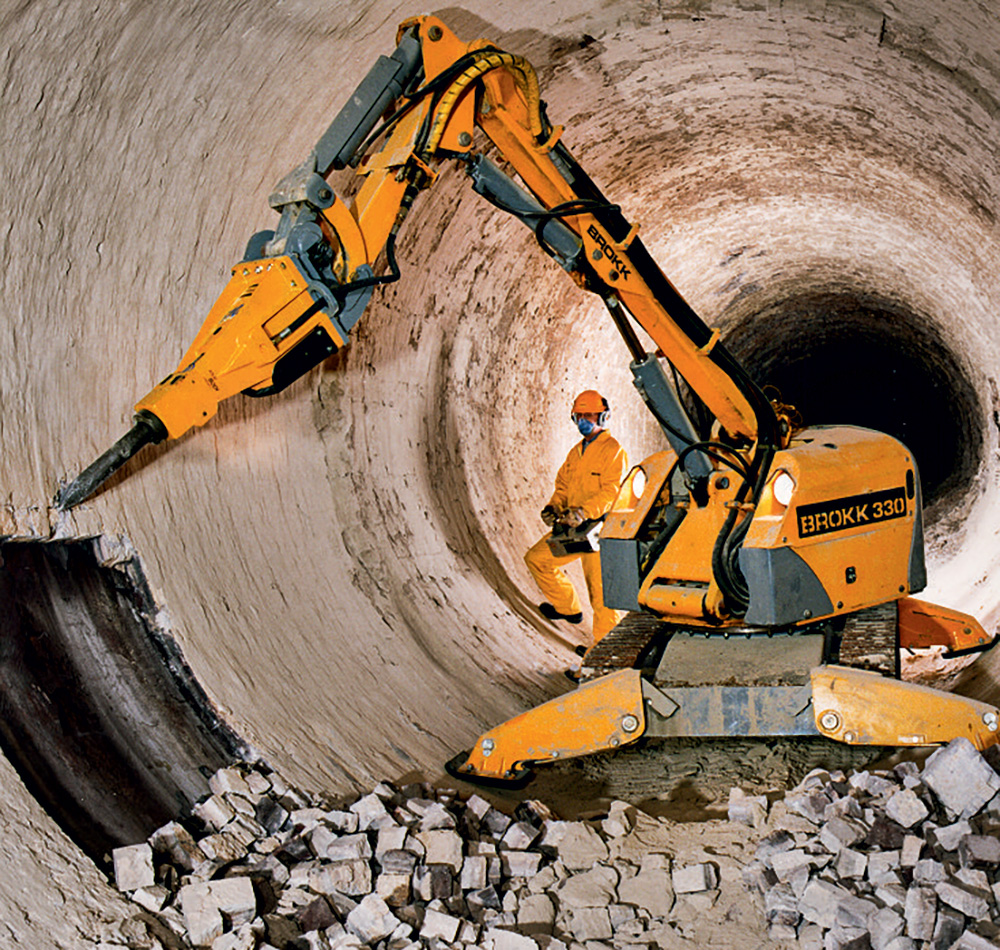
Introduction: The Challenge of Operational Safety in High-Temperature Environments
In industries such as steel manufacturing, cement production, and non-ferrous metal processing, operational safety is of paramount importance. Workers are exposed to high-risk environments, where extreme temperatures and hazardous materials can lead to equipment failure, accidents, and even catastrophic events if safety measures are inadequate.
Refractory materials, which line furnaces, kilns, ladles, and other high-temperature equipment, are essential for maintaining operational safety. Their role is not only to withstand intense heat but also to protect workers and equipment from dangerous conditions. In this case study, we highlight how Pennekamp Middle East’s advanced refractory solutions contributed to improving operational safety for a major industrial manufacturer.
The Client’s Challenge: Ensuring Safety in a Steel Manufacturing Facility
The client, a large steel manufacturer, was facing several operational safety challenges related to the performance of their high-temperature equipment. Their furnaces and ladles, which operated at extreme temperatures, were experiencing premature wear and damage due to thermal shock, slag corrosion, and mechanical stress. As a result, the safety of the workers was at risk, and production efficiency was compromised due to frequent shutdowns for repairs and maintenance.
Additionally, the facility had to meet stringent environmental and safety regulations, which included minimizing the risk of fires, explosions, and harmful emissions. Ensuring the reliability of their refractory materials was a critical step in improving safety and minimizing downtime.
Pennekamp Middle East’s Solution: Tailored Refractory Products for Enhanced Safety
Pennekamp Middle East was engaged to provide advanced refractory solutions that would address the client’s safety concerns and improve the overall efficiency of their operations. Our team conducted a thorough analysis of the facility’s operations, including assessing the existing refractory materials, identifying areas of improvement, and understanding the unique challenges of the steel production process.
Based on this analysis, we recommended a tailored solution that included:
- High-Performance Refractory Bricks: We supplied high-quality MgO-C bricks designed to withstand the extreme conditions inside the steel furnace and ladles. These bricks provide superior resistance to thermal shock, thermal cycling, and mechanical wear, helping to prevent cracks and damage to the equipment, reducing the risk of safety incidents.
- Customized Hot-Repair Mixes: To address wear and tear in high-stress areas, we provided specially formulated hot-repair mixes for the ladle and furnace linings. These mixes are designed to be applied without requiring the furnace to be shut down, allowing for quick repairs and reducing the risk of accidents caused by damaged linings.
- Advanced Castable Solutions: For areas prone to slag corrosion, we recommended high-quality refractory castables that offer enhanced slag resistance and durability. These castables protect the equipment from chemical attacks, reducing the likelihood of failures that could jeopardize safety.
- Comprehensive Training and Support: We also provided extensive training to the client’s maintenance teams on proper refractory installation, repair, and inspection procedures. Ensuring that personnel understood the importance of refractory maintenance played a crucial role in enhancing overall safety.
Results: Improved Safety and Increased Efficiency
The implementation of Pennekamp Middle East’s advanced refractory solutions led to significant improvements in operational safety at the steel manufacturing facility:
- Reduced Risk of Equipment Failure: The high-performance refractory materials significantly reduced the risk of thermal shock, mechanical damage, and slag corrosion. This led to fewer incidents of equipment failure, which previously had posed a safety hazard to workers.
- Enhanced Protection for Workers: By improving the integrity of the furnace and ladle linings, the facility was able to reduce the likelihood of dangerous incidents, such as hot metal spills, fires, and explosions. The workers were better protected from hazardous situations.
- Minimized Downtime: The tailored hot-repair mixes allowed for quicker and more efficient repairs, reducing downtime for maintenance. This helped the facility maintain smooth operations without compromising safety.
- Compliance with Safety Regulations: By adopting our advanced refractory solutions, the facility was able to meet and exceed industry safety standards and regulatory requirements, ensuring that operations remained compliant with environmental and safety guidelines.
Conclusion: The Role of Advanced Refractory Solutions in Operational Safety
This case study demonstrates how advanced refractory materials can play a crucial role in improving operational safety in high-temperature industries. By selecting the right refractory solutions and ensuring proper installation and maintenance, companies can reduce risks, prevent accidents, and enhance the safety of their workforce.
At Pennekamp Middle East, we understand the critical role that refractories play in ensuring the safety, efficiency, and longevity of industrial operations. Our high-performance refractory products are tailored to meet the unique needs of each client, providing long-lasting protection and support for high-temperature processes.
Contact Pennekamp Middle East today to learn more about how our advanced refractory solutions can help improve the safety and efficiency of your operations.