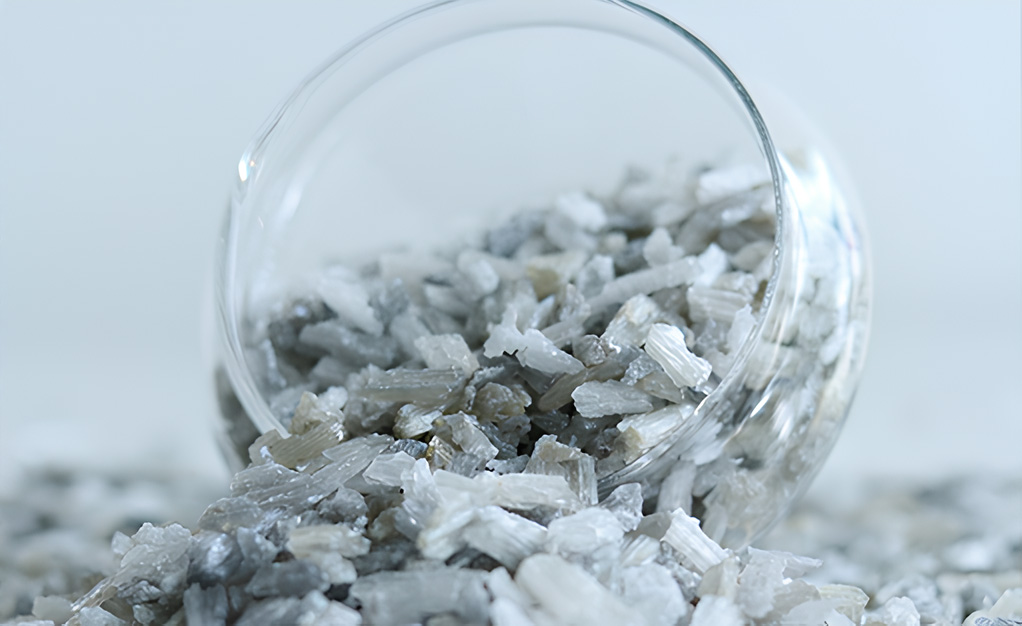
In the realm of high-temperature industrial applications, the choice of refractory materials can make or break the efficiency and longevity of your equipment. Among the wide range of materials available, fused mullite stands out for its remarkable properties and versatility. This blog delves into what makes fused mullite an indispensable material for industries that operate in extreme conditions.
What is Fused Mullite?
Fused mullite is a synthetic refractory material composed primarily of alumina (Al2O3) and silica (SiO2), with a unique crystalline structure that gives it exceptional stability at high temperatures. It is produced by melting a mixture of high-purity raw materials in an electric arc furnace, followed by controlled cooling. This process results in a highly dense, homogeneous material with minimal impurities, making it ideal for demanding industrial applications.
Key Properties of Fused Mullite
Applications of Fused Mullite
Thanks to its robust properties, fused mullite finds application in a variety of industries:
Why Choose Fused Mullite?
Choosing fused mullite for your high-temperature applications offers several benefits:
Conclusion
Fused mullite is a material that exemplifies the best in refractory technology, offering unparalleled performance in high-temperature environments. Whether you’re in the glass, steel, ceramics, or petrochemical industry, fused mullite provides the reliability and durability needed to keep your operations running smoothly. At Pennekamp Middle East, we are committed to supplying high-quality fused mullite that meets the stringent demands of modern industry, ensuring you get the most out of your high-temperature applications.