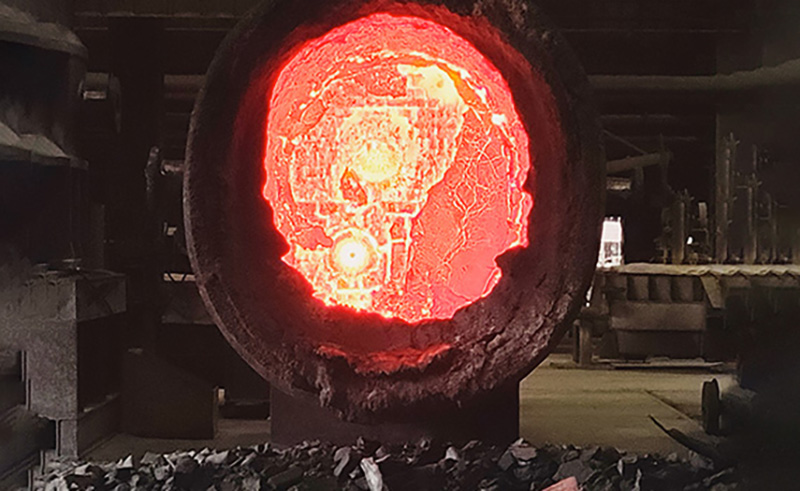
The steel production process is an intricate dance of intense heat, molten metal, and specialized equipment. While the colossal blast furnaces and towering casting bays often steal the spotlight, a less conspicuous but equally crucial player sits quietly behind the scenes: the ladle furnace. This workhorse vessel plays a vital role in ensuring the quality and consistency of molten steel, and its efficient operation relies heavily on a specific type of refractory material – ramming masses.
What are Ramming Masses for Ladle Furnace?
Ramming masses are precisely formulated dry refractory materials designed to be compacted and shaped into desired configurations upon installation. They are a versatile solution for various applications within the ladle furnace, offering several advantages over pre-fired refractory shapes:
Composition of Ramming Masses for Ladle Furnace:
The specific composition of a ramming mass for ladle furnace applications varies depending on the intended purpose and operational requirements. However, some common components include:
Key Properties of Ramming Masses for Ladle Furnace:
To effectively perform in the demanding ladle furnace environment, ramming masses must possess several key properties:
Applications of Ramming Masses for Ladle Furnace:
Ramming masses serve a variety of purposes within the ladle furnace, each requiring a formulation optimized for specific performance demands:
Pennekamp Middle East: Your Partner for High-Performance Ramming Masses for Ladle Furnace
Pennekamp Middle East is a leading provider of high-quality ramming masses specifically designed for ladle furnace applications. We understand the diverse requirements of different ladle furnace zones and offer a comprehensive range of formulations to meet your specific needs. Our team of refractory experts can assist you in selecting the optimal ramming mass