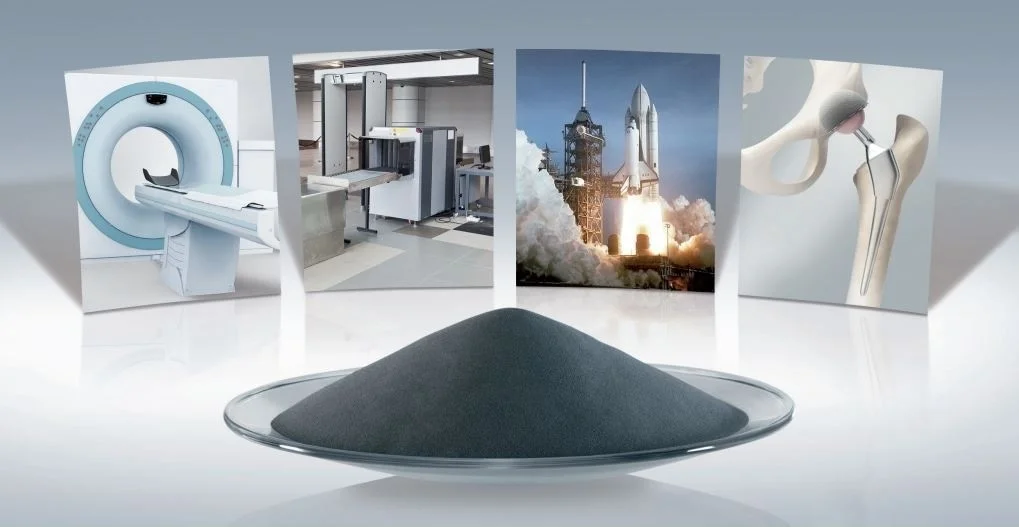
The traditional landscape of refractory manufacturing is undergoing a transformation with the emergence of 3D printing technology. This innovative approach offers exciting possibilities for creating complex shapes, reducing waste, and optimizing performance in various refractory applications.
The Evolving Landscape of Refractory Manufacturing
For decades, the production of refractory materials has relied on established techniques like casting, pressing, and machining. While these methods have served the industry well, they come with limitations, including:
Introducing 3D Printing: A Game-Changer for Refractory Production?
3D printing, also known as additive manufacturing, presents a revolutionary approach to creating complex objects layer by layer. In the context of refractory manufacturing, this technology offers several potential benefits:
The Road Ahead: Challenges and Opportunities
While 3D printing holds immense promise for the future of refractory manufacturing, it is essential to acknowledge the existing challenges:
The potential of 3D printing in the realm of refractory manufacturing is undeniable. While challenges remain, ongoing research and development efforts hold the key to unlocking its full potential. Pennekamp Middle East, as a leading provider of refractory solutions, is committed to staying at the forefront of this evolving technology. We are actively exploring the possibilities of 3D printing and its potential to revolutionize the industry.
Stay tuned for further updates on our exploration of 3D printing in refractory manufacturing. In the meantime, feel free to contact us to discuss your specific refractory needs and how we can help you achieve optimal performance and efficiency.